7 Smart Vertical Grow Room Design Tips for Maximum Yields
Upgated: July 4, 2025 · 21 min read
In the modern growing industry, vertical grow room design is no longer just a trendy term, but the key to yield and efficiency. It provides a shortcut to efficient production for growers who want to maximize yield in a limited space.
In the past, growers often used “flat thinking” for planting layouts. Now, rising real estate costs and better environmental control technology are pushing them to look “up.” Vertical planting greatly expands the planting area. It also helps control temperature, humidity, light, and airflow. More importantly, it represents a shift in the future of growing - smarter, more energy efficient, and more controllable.
Are you concerned about using your limited growing space? Do you want to set up an efficient, easy-to-maintain, and scalable grow room? If so, this article will inspire you. We’ll share the key elements of vertical grow room design. This includes core principles, layout examples, and energy-efficient HVAC solutions.
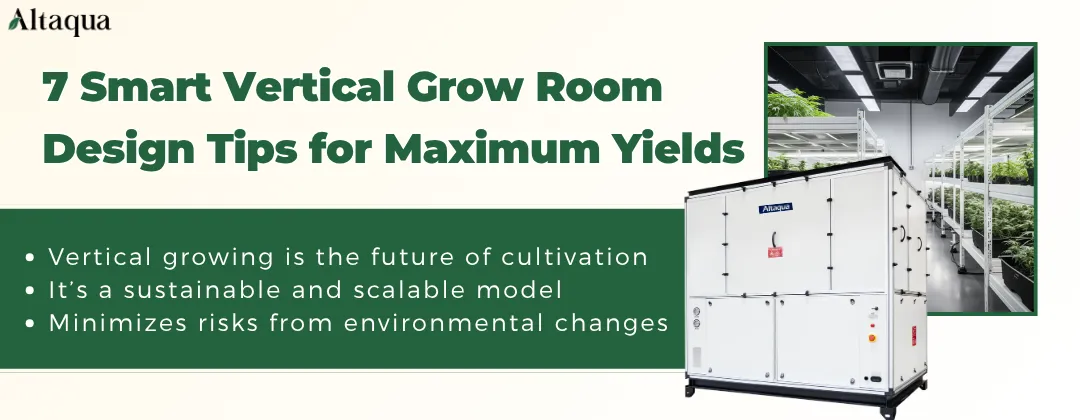
The Benefits of Vertical Grow Room Design
In the modern grow industry, space is capacity. Choosing a vertical grow room design goes beyond repurposing space. It's about efficiency, energy use, and technology integration. Here are three areas that demonstrate the practical benefits of a vertical grow room design.
Maximize Canopy In Limited Footprint
A big benefit of a vertical grow room design is that it lets you create “growing layers” in a small area. By using multiple tiers of planters, growers can turn every inch of space below the ceiling into capacity. This layout works great for urban grow programs, high-rent areas, or any commercial facility that wants to boost production without needing more space.
For example, in a traditional floor plan layout, a 1,000-square-foot grow room can only accommodate up to one tier of plants. With a three-tier vertical grow room design, the same space can be converted into 3,000 square feet of growing area. The capacity grows quickly without raising rent, utilities, or management costs. This is key for commercial growers looking for a high return on investment.
In addition, the vertical grow room design provides a more logical path for the placement of light, ventilation, and other systems. Raising plants and bringing light sources closer can cut energy use. This also boosts how well light energy is used. Breakthroughs in space efficiency lead to better yields and higher revenues per unit area.
Enable Scalable And Energy-Efficient Growth
Another key advantage of vertical grow systems is their scalability and energy efficiency. Once a traditional grow room is built, its structure is often difficult to adjust. Vertical systems are usually modular. You can easily set up, add, or take away equipment like grow racks, lights, or HVAC parts. This lets you adjust to your changing production goals.
Many growers use grow mobile systems or grow carriages installed on rail systems to allow racks to move smoothly and safely. These setups often have anti-tip rail technology. This keeps operations stable and secure during daily movement. This mobility makes it easier to reach different crop levels. This reduces cycle time and improves workflow, especially in high-density rooms.
This mobility also helps maximize canopy space without compromising on safety or ease of maintenance. As a result, growers can expand quickly based on sales or order volume without having to redesign the entire space. For example, you might only use two vertical tiers at first and leave the third one empty. Later, when demand increases, you simply add light fixtures and ductwork to activate that level—no need to re-lease or build a new facility. This flexibility helps lower operational costs and upfront investment.
Additionally, a well-designed energy-efficient system can significantly reduce daily energy use. Centralized lighting and air conditioning save energy. They are placed close to plants, which helps provide even coverage. Zoning your HVAC and dehumidification systems means you only run what’s needed, cutting waste and protecting crop quality. These strategies boost energy efficiency. They also cut labor costs by improving planning and making maintenance easier.
Improve Environmental Precision And System Integration
The tiered design of the vertical grow room adds complexity to environmental control. However, it also offers unmatched precision in control. Growers can use advanced sensor networks and automation systems. They can set different target values for temperature, humidity, CO2 levels, and VPD for each layer. This helps ensure that all plants thrive in the best growing conditions.
For VPD, a traditional layout might need just one sensor to watch the whole space. But in a vertical system, airflow and temperature change on each level. This makes layered monitoring very important. Growers can install multiple sensors linked to a central control system. This setup lets them adjust wind speed, dehumidification, and light intensity for each layer in real time. They can respond to different plant growth stages or sudden changes in the environment.
What's more, vertical systems facilitate equipment integration. Altaqua's top HVAC systems link easily to dehumidifiers, air delivery systems, sensor platforms, and Wi-Fi remotes. This integration makes your growing environment smarter and more automated. The system centralizes everything, from responses to data analysis. This cuts down on manual work and boosts operational efficiency.
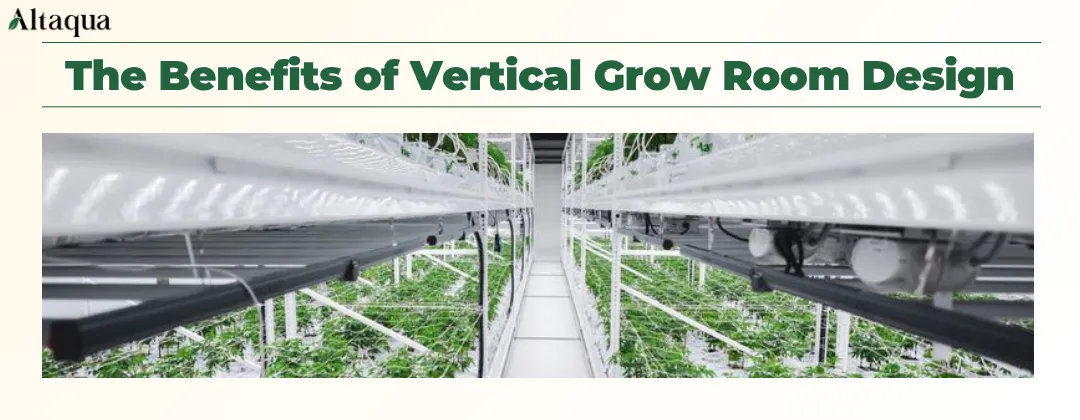
While maximizing space and yield, vertical grow rooms must also be designed for compliance. In various areas, governments set limits on plant counts for commercial planting. This includes the total number of plants per license and how closely they can be planted in a given area. Before expanding vertically, growers must check local regulations. This ensures their system design and operation stay within the license limits.
Many regulations set a specific plant count. So, even if you have space, growing more than allowed can lead to licensing risks or fines. Growers can expand easily by controlling the design stage. A modular and adjustable equipment setup helps them stay compliant. This not only demonstrates business agility, but also lays the foundation for sound long-term growth.
Core Principles of Vertical Grow Room Design
Creating an efficient vertical grow room design is not simply about stacking plants on top of each other. It's a tricky process. It needs careful planning. This helps with short-term productivity and long-term growth. A good vertical grow room design balances space use, airflow, and system efficiency. Without balance, problems like microclimates, uneven canopy growth, or HVAC overloads can happen fast. Three core principles are key to a successful vertical grow room design. They create a setup that ensures steady yields and a stable growing environment.
Vertical Structuring: Rack Height, Tier Spacing & Accessibility
In vertical growing, the planting frame design affects how well the space works. The first is the planning of layer height and planting spacing. If the tiers are too close together, light, air, and maintenance space suffer. But if they are spaced too far apart, you waste valuable vertical height.
An ideal design should set the spacing of each layer according to the growth cycle and final height of the crop. For example, use a compact design during the nutrient stage. Then, provide more space during the flowering stage so the plants can stretch. Also, to make daily tasks easier, leave enough space between each layer. This way, workers can see, prune, or harvest the plants. If needed, create a movable platform or lifting system to boost efficiency and safety.
A reasonable vertical structure also needs to take into account water, electrical and plumbing wiring. An overly complex inter-storey structure may lead to maintenance difficulties and safety hazards. Therefore, a simple, well-organized and maintainable structure is the first step to the success of every vertical grow room.
Airflow Logic: Avoiding Microclimates Between Layers
Multi-storey planting structures boost productivity. However, they can also create “microclimates.” These are differences in temperature, humidity, or gas concentrations between layers. Such unevenness can affect the uniformity of plant growth and even induce pests, diseases or localized mold.
In order to avoid this problem, the ventilation system must be designed using a logical “inside-out” approach. The first step is to make sure that air flows well through each layer, rather than being trapped between layers. Common approaches include ventilation channels between planting racks, low-pressure ducts to deliver cool air to the lower tiers, and multiple tiers of air speed and temperature and humidity sensors for dynamic adjustment.
Also, HVAC systems with EC fans can change air speed and volume automatically. They use real-time feedback to keep a consistent environment between tiers. Good airflow management helps plants transpire better. It also aids the HVAC system by providing more even cooling and dehumidification. This leads to stable and high crop yields in the room.
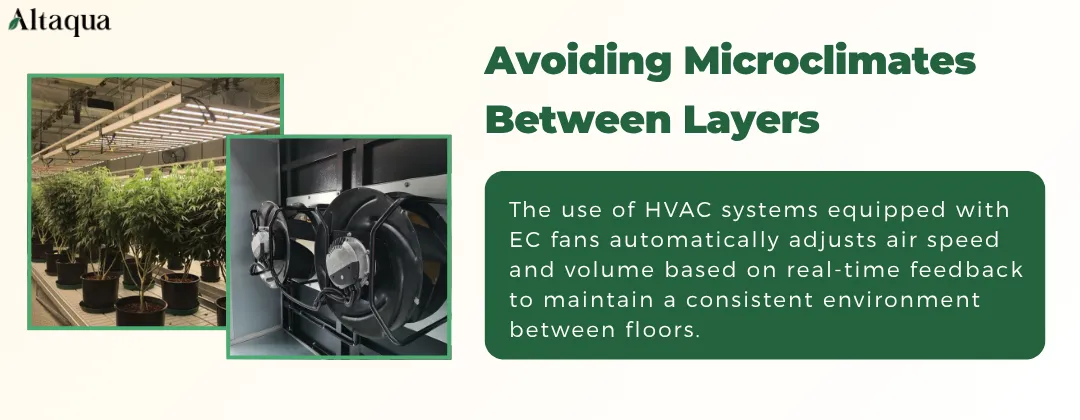
Load Planning: HVAC Load Distribution in Multi-Tier Setups
In multi-story buildings, HVAC systems encounter more challenges than those in single-story ones. Each floor gives off heat, moisture, and CO₂. These elements stack up vertically. This can create unbalanced loads in the space. As a result, the system's overall efficiency is affected.
This requires scientific planning of loads during the design phase. The first step is to perform thermal load simulations to predict the total amount of heat and moisture generated at each level. Next, calculate the cooling, heating, and dehumidification needs for each zone. Base this on the grow rack layout, fixture setup, and crop type. Then, allocate these needs wisely to the HVAC system.
Smart designs often put HVAC supply vents in different spots. This helps spread heat and cold evenly. They also use control systems that manage each level on its own. Some advanced systems also support dew point control. They help growers adjust VPD linkage. This leads to better environmental management. This not only improves crop consistency, but also helps extend equipment life and save on energy bills.
Equipment Integration in Vertical Grow Rooms
Vertical growing allows for “upward growth,” but it makes equipment setup more complex. In small spaces, achieving stable climate control needs careful planning. You must coordinate air circulation, humidity management, and remote control effectively. In this section, we will explore the main elements and strategies for optimizing equipment in vertical growing environments.
HVAC & Dehumidification: Compact Systems for Vertical Environments
In a traditional single-story grow room, the size and location of HVAC equipment is often not an issue. But in vertical grow structures, every inch of space is valuable. So, choosing HVAC and dehumidification systems with compact, modular designs is the first step for efficient integration.
HVAC systems for vertical environments are typically characterized by two features: compact dimensions for easy wall or ceiling mounting, and integrated functionality, with temperature, humidity, and dew-point control all in one system. An integrated dehumidification heat pump can dehumidify, cool, and circulate air all at once. This means you don’t need several units running together. As a result, it cuts down on energy use and maintenance costs.
For large planting facilities, use a multi-module layout. This setup helps avoid the “heat island effect.” It also allows for zone-by-zone adjustments and improves the overall environment.
Airflow Mapping & Return Placement
In vertical structures, the design of airflow paths must be more scientific. Multi-storey racks can create dead corners or stagnant areas between floors. If the air supply and return are not planned well, it can lead to different environments on each floor. This difference can affect how evenly crops grow.
Use top-feeding with side-returning or directional air-feeding. Also, consider a multi-point air-returning layout. The air supply should move horizontally across the plant canopy. This helps remove heat and moisture. Then, it should return air from the end of each layer or row. This can avoid the lower air being suppressed and retained by the upper air, thus improving the ventilation efficiency.
Also, simulate air flow when designing air ducts. This helps avoid blind spots and prevents fast airflow from hitting plants. You can boost how quickly the environment responds by installing adjustable air outlets or variable speed fans correctly.
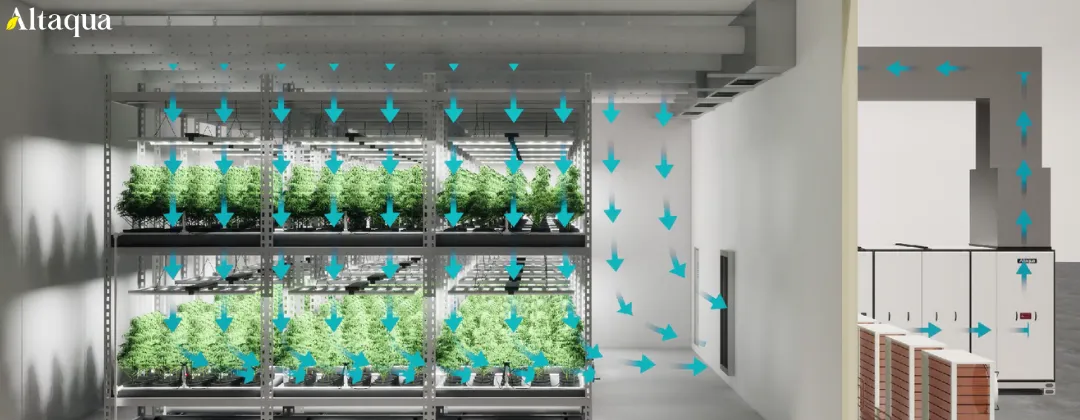
VPD Zoning & Sensor Distribution
In vertical growing environments, monitoring is key. Light, airflow, and moisture can differ from layer to layer. Using VPD (Vapor Pressure Difference) as the main control variable helps growers. It balances temperature and humidity better. This approach improves transpiration efficiency and boosts nutrient uptake.
It's best to do VPD zoning layer by layer. Each layer should have at least one temperature and humidity sensor, plus one leaf temperature sensor. In areas with big temperature differences, like near HVAC vents, doors, windows, or corners, add more points to collect real-world data.
Linking the HVAC system to sensors with dew point control algorithms allows for finer environmental adjustments. For example, if a floor has high humidity and temperature, the system can boost dehumidification and ventilation there. This happens without impacting other floors. This precise control helps create a truly consistent and replicable vertical growing environment.
Irrigation & Drainage – Gravity-Aware Design Choices
In vertical farming, how water is distributed and recovered matters. It affects both resource use and plant health. Because of the stacked layout, gravity flow becomes a critical factor when designing both irrigation and drainage. A well-designed system must ensure even water delivery across all vertical levels and prevent excess runoff or equipment leakage.
Drip irrigation is the most commonly used method due to its precise control over water volume, significantly reducing the risks of overwatering and underwatering. For growers using hydroponic systems, it’s especially important to balance water pressure across tiers. Without careful planning, lower levels might get too much water. Meanwhile, upper levels may not get enough. This imbalance can lead to inconsistent crop development and root-related issues.
To optimize the irrigation setup, it’s recommended to install separate irrigation supply points for each level, allowing independent control over timing and flow rate. Adding humidity or moisture sensors to these systems creates a "water-on-demand" strategy. In advanced setups, the irrigation system can be integrated with controlled environment agriculture (CEA) platforms, adjusting output automatically based on real-time environmental data—enhancing both efficiency and system intelligence.
Drainage design is equally important. In a vertical layout, poor drainage can lead to cross-contamination between layers. Excess water may drip down and create high-humidity pockets or pathogen spread across lower tiers. To avoid this, each level should include its own drainage tray or a sloped return system that directs water back to a centralized drain. For hydroponic operations, a closed-loop system with filtration is ideal to minimize water waste and support reuse.
Control Systems: Wi-Fi Climate Control & Remote Monitoring
Efficient device integration is not possible without an intelligent control system. Especially in multi-layer environments, it is almost impossible to respond in real time with manual adjustments. A stable, easy-to-use, and remote climate control platform is very important here.
Growers in modern vertical grow rooms are increasingly choosing Wi-Fi connected control systems. These systems let them check important data like temperature, humidity, VPD, dew point, and system load anytime. They can access this information through a mobile app or web backend. Some top-tier systems support chart analysis, data export, and history playback. This helps growers evaluate and adjust environmental trends easily.
More advanced systems also support zone control and remote alarm functions. For example, if humidity suddenly rises in an area, the system can quickly send a text or email alert. It also lets you switch operation modes or turn on backup dehumidifiers remotely. This design greatly improves the response speed and also guarantees the consistency and safety of planting.
In addition, the openness and compatibility of the control system is also very critical. Pick a platform that supports common protocols like Modbus or BACnet. This choice connects your grow room equipment, such as lighting, irrigation, and CO₂ systems. It also sets the stage for future upgrades and automation.
Space Optimization Tips From HVAC Experts
In a vertical grow room, every cubic foot is precious. Every facility designer must consider how to create an efficient layout. They also need stable climate control and easy maintenance, especially in limited spaces. This advice comes from seasoned HVAC engineers. They help customers balance space and environment daily.
Layering Without Overloading HVAC Zones
When designing multi-tier grow racks, many people mistakenly focus only on adding more tiers. They often overlook the load limits of the HVAC system. As a matter of fact, each additional tier means more light heat, higher humidity release, and more complex air flow paths.
It’s best to plan your zoning around the total HVAC capacity first. Then, you can design the number of floors. Generally, don’t exceed two shelf heights for one HVAC partition. This rule applies unless you use an ultra-high airflow system with multi-point supply and return air design. Zones are set for different levels. Each zone has its own air supply, return paths, and sensors. This setup helps prevent "overheating" on the upper level and "humidity" on the lower level.
Also, leave enough space between the layers. This lets air circulate well and makes it easier for maintenance staff to work. This not only protects the plants from environmental fluctuations, but also extends the service life of the equipment.
Ensuring Even Humidity & Temperature in Every Cubic Foot
One of the biggest challenges in a vertical grow space is keeping the climate conditions on the “top, middle and bottom” levels consistent. Many new installations work well at first. But over time, growers notice some issues. Some layers become wet and waterlogged. Plants on the lower levels grow slowly. Also, temperatures at the top stay high.
To address these situations, the key to HVAC design is: precise airflow layout + layered sensing and monitoring. Use a multi-point air supply system. Place air outlets along the sides of the grow frame. This way, airflow will cross each canopy layer. At the same time, the return air outlet should be set on the opposite side of the wind to form an effective “convection channel”.
For humidity control, set the return air point of the dehumidification unit in the middle or lower layers. This helps to easily remove moisture that collects at the bottom. With VPD sensors, dew point sensors, and leaf temperature sensors, we can monitor different locations in real-time. The system then uses algorithms to adjust air volume and cooling in each area. This helps achieve a dynamic balance.
Remember: even just one or two cubic feet of temperature and humidity imbalance can trigger mold, disease, or uneven growth. That's why equilibrium is not an ideal state, but the foundation of successful vertical growing.
How to Design for Easy Maintenance & Future Scalability
Many facilities aim for compactness and try to fit in as much as possible at the start of construction. However, after six months, the demands of operation and maintenance become clear. For example, changing filters means taking out whole rows of plants. Inspecting condensate lines needs drilling into tight spaces. Also, there are no pre-made connections when adding equipment.
To avoid these issues, consider maintenance access, service openings, and extra space for equipment when you design. Critical parts of the equipment, such as air intakes, drains, and control panels, should be reserved for at least 60cm of workspace. Electrical and drainage lines should be layered for easy inspection and future replacement.
When choosing HVAC hosts, consider modular products. They allow for easy expansion, even if you only install part of the system at first. Later, as your needs grow, you can quickly add more capacity. Also, the wiring and control system should have communication ports. This allows for future smart connections, remote control, or data sharing. It sets a strong foundation.
A "well-maintained" planting room saves time and labor. It also cuts operating costs. A "scalable" system makes your investment flexible. This way, it can grow with the market.
5 Examples of Vertical Grow Room Layouts
Vertical grow room designs can take many forms, each tailored to specific cultivation goals, space constraints, and climate control requirements. Choosing the right vertical grow room design depends on how you want to balance yield, workflow, and system integration. Below are 5 practical vertical grow room layouts, all rooted in proven vertical grow room design principles and applied in real-world commercial projects. These designs help maximize space efficiency while maintaining consistent environmental control across every level.
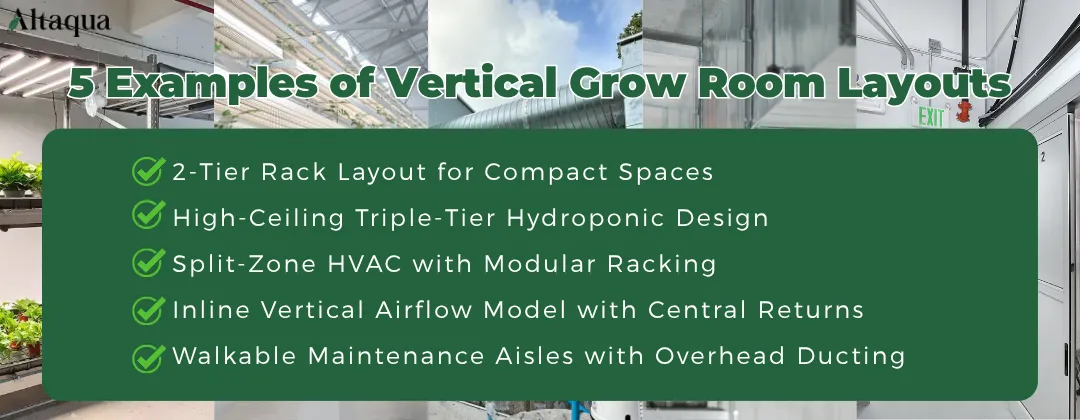
2-Tier Rack Layout for Compact Spaces
When you have limited growing space, such as a room the size of a garage, a double-tier grow stand is the safest, most maneuverable option. It doubles the yield right out of the box without adding pressure to the tier height. And since there are only two tiers, height control is relatively easy and air circulation is less prone to dead spots.
In this layout, place supply and return air on both sides of each layer. Also, use the circulating fan to keep air velocity even. The space between the upper and lower levels must fit lights, fans, and sensors. It should also allow personnel to move around easily. This layout is easy to start and needs little upkeep. It's perfect for beginner growers or small projects with tight budgets.
High-Ceiling Triple-Tier Hydroponic Design
If your space has a floor height of 14 feet (about 4.3 meters) or more, think about using a three-tier or taller grow rack with a hydroponics system. This setup helps reduce weight stress. This design works well for big commercial projects. It's ideal for grow rooms that convert warehouses.
The key to a three-tier structure is to maintain environmental consistency on each tier. Each tier usually has its own air supply ducts. Air comes from above, flows through the crop canopy, and then gets pulled back in by return air vents on the other side. The hydroponic system can fit neatly under the floor on each level. This setup helps with easy management and rehydration.
This layout puts a heavy load on the HVAC system. It also needs a denser sensor layout. This helps keep environmental differences between layers within the allowed range.
Split-Zone HVAC with Modular Racking
Zoned HVAC with modular grow racks offers great flexibility. This setup works well in large or oddly shaped facilities. It's also useful for places that need crop rotation. The space has small zones. Each zone controls its own temperature and humidity. This helps adjust the environment for different plant stages or varieties.
You can easily adjust the modular grow racks. Change their number and layout based on the season, batch, or variety. This won't affect the overall air supply system. This layout is particularly suitable for facilities that run nursery, flowering and mother plant zones at the same time.
One more benefit of the zoned design is that if a problem arises in one area, like a disease or equipment failure, it won't disrupt the whole system. This setup helps manage risks effectively.
Inline Vertical Airflow Model with Central Returns
This layout emphasizes linear airflow penetration and air renewal efficiency. Air enters from one end at the top of the rack. Air guides on each level spread the airflow evenly. Then, it is pulled back uniformly from the other end at the bottom. The central return air duct is often located on one side of the room or in the middle. It connects to the dehumidifier or air conditioning unit.
This layout needs higher air flow and balanced air pressure. Once it's set up and stable, it needs only a small circulation fan for natural convection. It's great for facilities aiming for energy savings or low-intervention operations.
It also helps with data collection. By placing one sensor before and after each floor, you can see the full climate dynamics.
Walkable Maintenance Aisles with Overhead Ducting
This layout is ideal for large-scale grows and dense equipment that require high levels of routine maintenance. A “walk-in tunnel” is provided between every two rows of planting racks, making it easy for staff to visit, change equipment or carry out cleaning work. The air supply system is located in the ceiling above, and the adjustable air vents evenly deliver cool air or dehumidified air to each level.
Air comes in from the top, while return air exits from the bottom. This creates "temperature and humidity layered control." It helps keep the upper floors' environment consistent. Maintenance aisles lower the chances of accidental contact, heat buildup, or CO₂ buildup during work.
This design uses a bit more space. But in the long run, it can lower failure rates, cut maintenance costs, and boost efficiency.
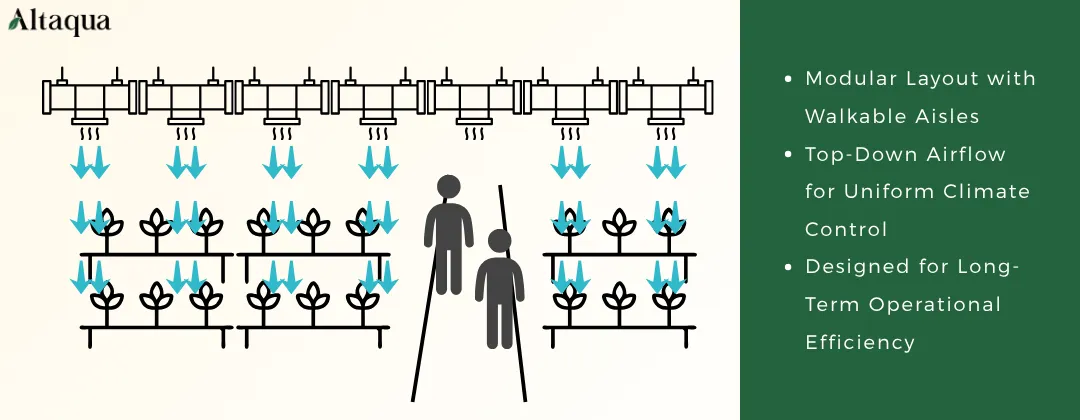
Cost & ROI Analysis: Is Vertical Grow Room Design Worth It?
Before deciding to adopt a vertical growing system, it's important to know its costs and payback cycle. Vertical growing usually requires a higher startup cost. However, it often saves money over time through better efficiency in operations and production. Below, we break down three key aspects to help you determine if this design meets your investment goals.
CAPEX vs. OPEX Breakdown
When it comes to capital expenditures (CAPEX), vertical grow systems typically have higher upfront costs than traditional horizontal grows. You may need to invest in customized multi-level grow racks, LED lighting, reinforcing structures, ductwork, and HVAC equipment to support air circulation on multiple levels. A standard HVAC system for a single-level grow room needs just one supply and return air setup. But a vertical structure requires layered air supply and advanced airflow control devices.
But it’s the daily operating costs (OPEX), not the one-time investment, that decide a project's profitability. Vertical structures can boost output by two to three times. This means you can plant more in the same space. As a result, costs for rent, utilities, labor, and maintenance get spread out more. Also, modern energy-saving tools like inverter dehumidifiers, EC fans, and smart controllers can optimize energy use. This leads to big savings over time.
Yield Per Square Foot Comparisons
This is where vertical growing has its most intuitive advantages. Traditional single-tier designs use 30-50% of indoor space for growing. In contrast, vertical grow racks boost that to 70-80%. By increasing the number of plantable tiers, a space of the same size can support more plants, even up to double or triple the original number.
In a 500-square-foot grow room, a traditional setup holds up to 150 plants. However, with a three-tiered vertical rack, you can fit over 400 plants. This multiplier effect boosts production value per square foot. As a result, it lowers the production cost per unit significantly. For high-value crops like indoor flowers or medicinal plants, the output gap can lead to huge profit growth.
Climate Control Efficiency Gains
Many people worry about whether vertical planting structures will add to the HVAC burden. The opposite is true - as long as the system is properly designed, it can actually improve climate control efficiency.
The vertical layout centers the air ducts and spreads air more evenly. This design lowers dead zones of temperature and humidity. It also prevents energy waste from the system's “over-compensation.” Next, the layered air supply system, like the Altaqua integrated dehumidification air conditioning, automatically adjusts air speed and cooling load for each layer. It uses only what is needed, which cuts down on energy waste.
With smart control systems, growers can track dew point, VPD, humidity gradient, and air speed changes. This lets them react quickly to make system adjustments. This precise control boosts crop quality stability. It also lessens equipment operation intensity. This helps extend service life and saves on maintenance costs.
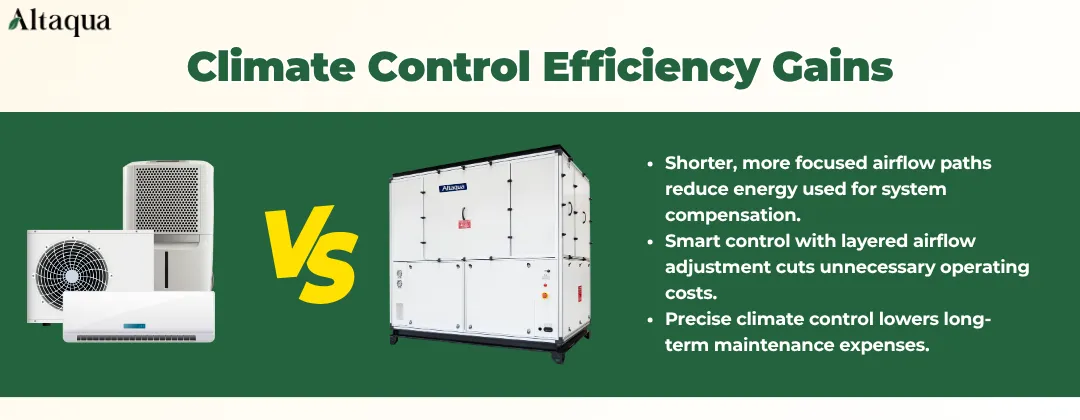
Altaqua Solutions for Vertical Grow Room Design
Altaqua, a manufacturer of HVAC systems for indoor growing, provides tailored solutions. We address the challenges of climate control, airflow layout, and energy efficiency in vertical growing. Every feature focuses on the main needs of multi-story buildings. This includes temperature and humidity control, duct layout, energy efficiency, and maintenance. These elements help growers maintain efficient and stable environmental control in tight spaces.
Precise Temperature and Humidity Control with VPD Monitoring
In vertical growing environments, temperature and humidity often vary from one level to another. This is especially true in densely packed areas with strong light, where conditions can change rapidly. Altaqua Grow Room HVAC system monitors and controls temperature and humidity in the growing space. It uses sensitive sensors and closed-loop control logic. This keeps the environment consistent throughout the area.
What's more, our devices have built-in VPD (vapor pressure difference) calculations in real time. Growers can see VPD readings in the grow room. This removes the need for manual conversions. It also helps them control irrigation and ventilation more precisely. This feature greatly boosts decision-making in growing plants. It’s especially important during rapid growth or when managing flowering.
Stable VPD = stable uptake, and stable uptake = more stable yield and quality. This is the dimension of control most valued by growers of high-value crops.
Custom Ducting Kits for Vertical Applications
In multi-story grow racks, air supply can be uneven. This often leads to overheating on top and overcooling below. Altaqua's high volume air supply design solves this problem. It works well with custom ductwork in grow rooms. This setup ensures even airflow and a consistent environment across all tiers.
Our equipment doesn’t include a ducting kit. However, many customers have successfully set up flexible ducting systems. They base these systems on floor height and planting density. This setup works well with our equipment. It greatly enhances airflow distribution efficiency. Ducts direct air to each layer of the grow area. This helps prevent localized climate issues and saves energy. It's especially important for vertical grow spaces that need precise environmental control.
This compatibility lets growers arrange the ducts based on their site needs. It ensures stable operation and even air flow. Plus, it makes maintenance and expansion easier. The Altaqua system works with air ducts. This combination boosts environmental control accuracy. It also offers a reliable way to save energy.
Energy-Efficient And Low-Maintenance HVAC For Vertical Grow Rooms
Multi-tier growing increases load densities and energy needs for HVAC systems. Altaqua's systems use high-efficiency compressors and inverter fans. These components work together with smart algorithms to cut down on unnecessary energy use.
We recognize that growers need “good maintenance.” Altaqua Grow Room HVAC system has easy-to-remove parts. So, changing filters is simple. Now, even a casual operator can do it without needing a skilled laborer. You can use the Wi-Fi remote control to check the system’s status from your phone or computer. This means you don’t have to visit the site daily to verify everything.
This system is designed to let you worry less about equipment and focus on crop management and yield optimization.
Conclusion
Designing a vertical grow room is more than just stacking plants. It’s about creating a smarter and more productive space for growing. This approach helps prepare for the future of agriculture. Vertical layouts help growers boost yield per square foot. They also allow better control over temperature, humidity, airflow, and lighting. The key is thoughtful planning—from rack spacing and airflow design to HVAC zoning and sensor placement.
Tiered grow systems provide scalability, energy efficiency, and better environmental control. These features lower operational costs and increase ROI. Modular layouts, automated irrigation, and climate systems help every layer of the grow room. They support healthy and consistent crop growth with smart airflow strategies.
The vertical grow room approach is flexible. It works for small two-tier systems or large commercial spaces with walkable aisles and integrated control systems. This method lets you expand and adapt easily. Plus, it helps you stay compliant while achieving high yields and long-term efficiency.
FAQ
1. Is vertical grow room design more expensive to set up?
Yes, the initial setup cost for a vertical grow room is generally higher than traditional single-tier systems. You’ll need to invest in specialized grow racks, compact HVAC systems, and precise environmental control equipment. However, the long-term savings from energy efficiency, higher yields, and better space use usually outweigh the upfront expenses.
2. How do I prevent environmental differences between grow layers?
Use a well-designed HVAC system with multi-point air supply and return paths, and install temperature, humidity, and VPD sensors on each tier. Good airflow design—like directional ducting, variable-speed fans, and real-time monitoring—helps keep climate conditions consistent across all layers.
3. Can I start with a small vertical setup and expand later?
Absolutely. Many vertical systems are modular by design. You can begin with one or two tiers and add more later as your needs grow. Just make sure your HVAC system and layout allow for future scalability, and leave access space for equipment and maintenance.
4. What crops are best suited for vertical growing?
Vertical grow rooms are ideal for high-value, fast-growing crops like leafy greens, herbs, microgreens, strawberries, and cannabis. These plants benefit from controlled environments and can thrive in dense multi-tier setups, especially with hydroponic or aeroponic systems.
Share with your friends:
Popular Blogs on Altaqua:
Download Catalogue