Mastering CFM for HVAC Efficiency and Cost Savings
Upgated: April 15 ,2025 · 22 min read
A vertical farm in Colorado faced heavy losses from a wilting top crop. The surprising diagnosis revealed that it wasn't due to the nutrient solution or light issues. Instead, the problem was an overlooked 400 CFM(cubic feet per minute) difference in the CFM HVAC system. This case showed a tough reality in today's environmental control. The exact control of CFM HVAC is now a hidden battleground. It can make or break facility agriculture.
In a growing environment, CFM HVAC control works differently than in a typical commercial building. It needs to control four main factors: temperature, humidity, CO₂ levels, and VPD (vapor pressure difference).
We will take you through the thermodynamic principles of dismantling, measured data comparison, etc., to master from the basic CFM HVAC calculation to artificial intelligence dynamic parameterization of a full set of optimization solutions, especially in the cultivation of marijuana and other demanding scenarios, how to achieve a 40% reduction in energy consumption through the fine control of CFM at the same time to improve crop yields ...
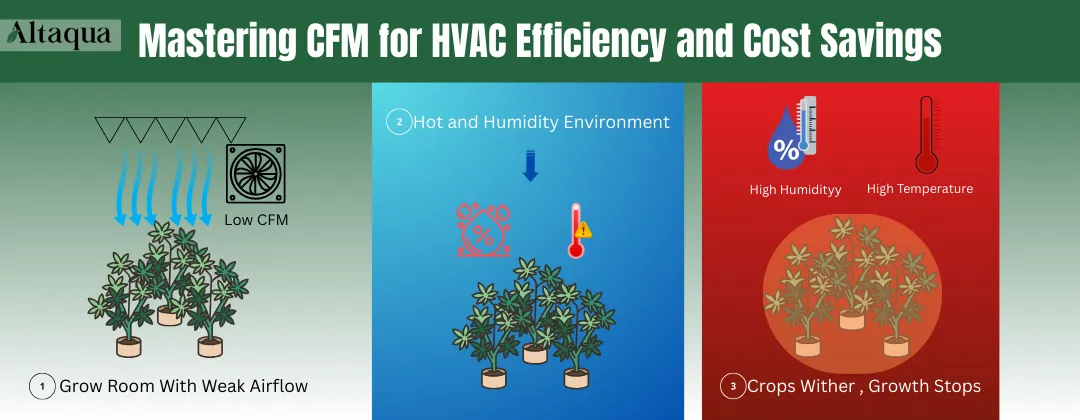
Why CFM HVAC Is Important for HVAC Efficiency
In an HVAC system, CFM (cubic feet per minute) measures how fast air moves. It impacts temperature control, humidity, and energy use. In grow rooms, incorrect CFM settings can harm plant growth. They can also increase energy costs and shorten equipment lifespan.
How Airflow Dictates Your HVAC’s Success
Airflow is the "blood" of the HVAC system. CFM shows how well the air flows. It matters for cooling, dehumidification, and heat exchange. The flow rate and air distribution impact the final result.
Understanding "Work Done on Air" in Cooling, Dehumidification, and Energy Transfer
In an HVAC system, air flows actively. It carries temperature, humidity, and energy. CFM shows how well air can "do work."
|
Define |
---|---|
Dehumidification |
Too much moisture in a growing space can cause mould. The right CFM lets air reach the cold surface in the evaporator. This boosts dehumidification efficiency. |
Cooling |
Enough CFM helps spread cool air evenly. This creates a balanced temperature in the grow room, preventing hot or cold spots. |
Energy Transfer |
Air flow efficiency impacts the refrigerant's heat exchange. If the CFM is too low, heat transfer suffers. This leads to lower system efficiency. |
Why Low CFM Restricts Airflow and Reduces HVAC Performance
CFM, or cubic feet per minute, measures how well air flows in an HVAC system. If the CFM drops below the design standard, the whole system works differently. If the actual CFM falls over 15 percent below the design value, the system has major problems. These issues affect air distribution, static pressure balance, and equipment lifespan.
In grow rooms, especially with vertical racks, uniform air flow is key. When CFM is too low, cold air doesn't spread well. This creates a temperature difference of over 3°F between the top and bottom of the rack. Such a gap is too much for cannabis plants. It can hurt transpiration and cause curling leaves and reduced photosynthesis.
Also, uneven humidity can happen. The top may be dry while moisture collects at the bottom. This lack of air movement raises the risk of mold and disease.
The situation is like having the air conditioning on but still feeling stuffy. Poor air circulation causes uneven heating and cooling in some spots. This directly impacts growth results.
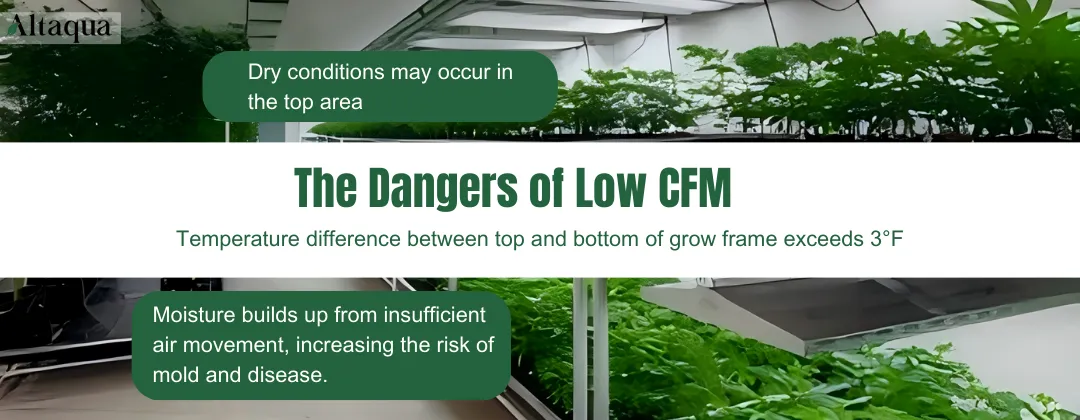
How Poor CFM HVAC Increases Operational Costs
Low CFM makes your HVAC system less efficient. It also increases operating costs, such as energy use, equipment wear, and maintenance.
Insufficient air movement slows down an HVAC system. It takes longer to hit the desired temperature or humidity. In a grow room with low CFM, cold air spreads slowly. If the sensor detects a temperature above the set point, the compressor keeps running. It will only stop when the target temperature is reached. This situation puts more strain on the compressor and also raises electricity costs a lot.
HVAC equipment relies on a steady airflow for heat exchange. If the CFM is too low, the heat exchanger works harder. This high workload for a long time can speed up wear on its parts. For example, condensate buildup can cause the evaporator and condenser to corrode.
This leads to lower heat exchange efficiency. Short cycling of the compressor can cause frequent starts and stops. This leads to more wear and tear. As a result, the service life shortens. Eventually, you may need to replace costly core components or the whole system.
3 Silent Dangers of Ignoring CFM HVAC
Ignoring CFM issues is like planting a time bomb in your facility. At first, you won't see the symptoms, but the damage will increase quickly. The following three major hazards can put your operation in crisis without warning.
Case Study: Mold Remediation Costs Due to Undersized Ducts
A customer chose a traditional HVAC system. It includes a 10-ton dehumidifier-cooler for their grow facility. But the construction team used an 8-inch return air duct. This was too small; the system needed a 12-inch duct. As a result, the CFM fell short of the design criteria.
At first, the system worked well during installation. But after a few weeks, problems popped up. Air distribution became uneven, and moisture built up in the grow room. Air got trapped in the ducts, and condensation couldn’t be cleared quickly. This led to mould on the walls and ceiling. Cannabis diseases also became common. Grey mould appeared on some leaves, hurting both yields and quality.
The homeowner had to quickly hire a team to fix a serious mold issue. They cleaned up thoroughly. This included pressure washing, spraying with antimicrobials, and replacing damaged materials. They replaced old 8-inch ducts with new 12-inch ones. This retrofit met code and improved airflow. This process took two weeks. The grow facility had to shut down, which caused a loss of profits from one harvest.
The main issue was undersized ducting. This led to lower CFMs and poor air circulation. For commercial grow facilities, good duct design and CFM compliance are vital. They help prevent moisture build-up and mould growth. If problems arise, fixing them will cost much more than investing in proper design from the start.
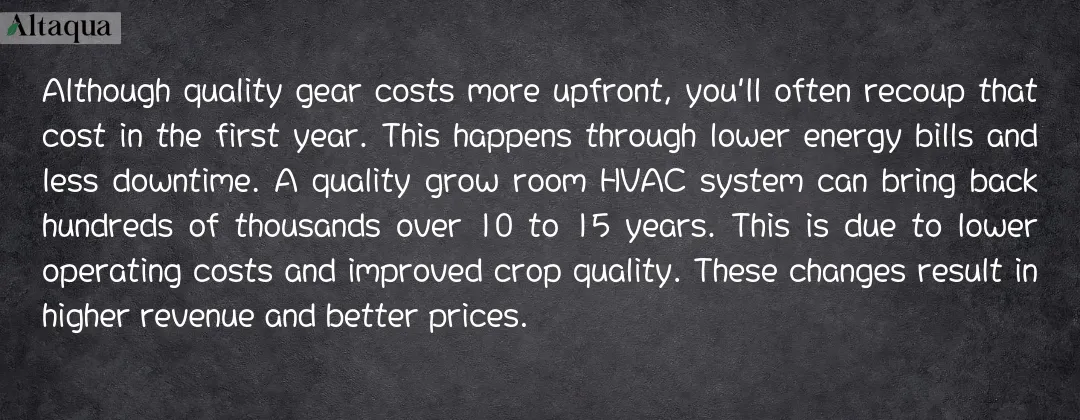
Evaporator Icing and Energy Efficiency Loss
When the HVAC system runs in the growing room, low CFM can cause weak air flow on the evaporator. This slows down water evaporation, leading to frost and ice build-up. This ice slowly builds up on the evaporator fins. It blocks air flow and cuts down cooling power. When cooling efficiency drops, the temperature in the growing room can’t stay in the set range.
Ice on the evaporator can make the system go into defrost mode. This shuts the system down, which affects the growing room environment and the plants' growth conditions. Many growing room operators don’t know that ice on the evaporator may cause issues. They usually realize it only when they see less cooling, strange equipment behavior, or high humidity.
The Impact of Temperature Fluctuations on Crop Growth
Plants react strongly to temperature changes. This is true for valuable crops, like cannabis and tomatoes. They grow well in controlled environments. They require constant temperature and humidity conditions to maintain optimal growth. If the CFM isn’t set right, the air flow becomes uneven. This can cause big temperature changes in the growing room. Such fluctuations directly impact the plants' metabolism.
Fluctuating temperatures can impact photosynthesis. When leaf temperatures rise too much, the stomata close. This limits CO₂ absorption and reduces the production of photosynthetic products. At the same time, transpiration will also be unbalanced due to temperature changes. An unstable water supply can cause leaf dehydration or water retention. This affects how well the plant's roots absorb water and slows down growth.
CFM Calculation Method and Practical Application
The CFM of your HVAC affects air circulation, temperature, and humidity in your cannabis grow room. If the CFM isn’t right, you might get uneven airflow and humidity buildup, which can harm crop growth. It's important to know how to calculate CFM per tonne of cooling. You should also adjust it for different environments to keep your grow room running well.
CFM Calculation Method and Application Range per Ton of Cooling Capacity
In the HVAC industry, CFM is often used to calculate cooling capacity per ton. A common empirical formula is as follows:
CFM = (room volume × air change rate) / 60
The air change rate varies with crop type and humidity needs. It helps estimate the basic air supply needed for the growing room. You typically need 400 CFM of air for each ton of cooling. However, you might need to adjust this in real situations.
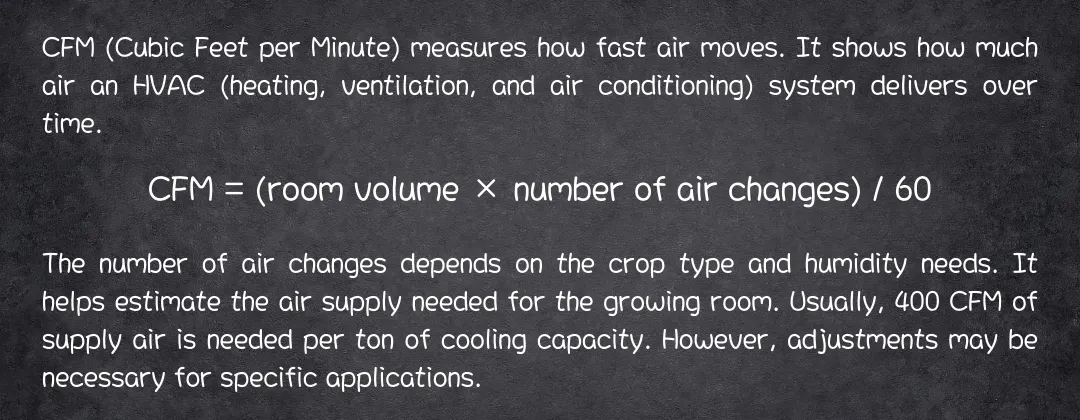
Change Requirements for Equipment Parameters and Practical Applications
Humidity, airflow, and condensing loads impact CFM calculations. So, grow room HVAC designs must be adjusted.
In humid places like grow rooms and greenhouses, plants release water by transpiration. This raises the air's moisture, which boosts the dehumidification load. If the CFM is too low, moisture can build up. This may cause mold and raise disease risks. To fix this, you can increase the CFM or add separate dehumidifiers.
In areas with small temperature changes, like grow rooms at night, the cooling load decreases when the lights turn off. However, humidity issues still exist. While CFM needs go down, you must adjust fan speeds for better air circulation. This helps maintain airflow and ensures the dehumidification works well.
In hot, busy environments like a grow room, equipment like lights creates a lot of heat. This raises the temperature and increases the need for airflow (CFM). To manage these changes, variable speed fans, such as EC fans, can adjust airflow based on the load. This helps improve system efficiency.
Comparison of CFM Reference Values in Different Environments
CFM needs change based on the environment. Here’s a comparison of reference values for different situations:
Application Scenario |
CFM Calculated Empirical Values |
Note |
---|---|---|
General growing room (standard load) |
400-450 CFM/Ton |
Suitable for environments with stable temperature and humidity and low loads |
High humidity grow room (high dehumidification load) |
450-550 CFM/Ton |
Requires higher air delivery to remove moisture |
High-temperature, high-load grow room (strong light conditions) |
500-600 CFM/Ton |
Need more airflow to maintain temperature equalization |
Precision controlled environment (lab-grade cultivation) |
350-400 CFM/Ton |
Suitable for high-end growing environments with fine control of temperature and humidity. |
These reference values help estimate in the early design stages. Further optimization is needed based on temperature, humidity, planting equipment layout, and airflow.
Industry Standards for CFM HVAC Calculation
In HVAC design, ASHRAE (American Society of Heating, Refrigerating and Air-Conditioning Engineers) and EPA (U.S. Environmental Protection Agency) set important standards. These guidelines help calculate CFM. They ensure air movement meets energy efficiency and air quality needs.
ASHRAE provides CFM values for different settings. It also lists ACH (Air Changes per Hour) ranges. For grow rooms, 30-60 air changes per hour are advised. This helps supply carbon dioxide. It also controls temperature and humidity. Plus, it keeps the air fresh.
The EPA cares about air quality. They recommend using air filtration systems rated MERV-8 or higher. Also, it's important to have enough CFM to cut down on contaminants. This helps stop mould and germs from growing.
Grow room HVAC designs usually follow ASHRAE and EPA guidelines. They also adjust to meet specific growing needs. This way, they ensure the system works its best.
Simple CFM HVAC Calculation Tools and Measurement Methods
In HVAC design and maintenance, measuring CFM (cubic feet per minute) is key. It helps control airflow, temperature, and humidity. To do this well, use the right tools and methods. This way, you can check if your HVAC system works as it should.
Introduction of Measurement Tools
To measure CFM, use tools like anemometers and manometers. These tools check wind speed and pressure changes in the duct. Then, they help calculate air flow.
Typology |
Name |
Function |
---|---|---|
Anemometer |
Hot Wire Anemometer |
Measures air speed by sensing temperature changes from air flow. This is useful in low air velocity areas like HVAC supply or return vents. |
Anemometer |
Vane Anemometer |
Measures wind speed by rotating an impeller. This tool works well in high wind areas, like air supply ducts or outlets. |
Anemometer |
Multi-Point Anemometer |
Great for measuring big air supply areas, giving better average air velocity values. |
Manometer |
U-Tube Manometer |
Used to measure the static pressure difference, it can help to calculate the air flow rate in the duct. |
Manometer |
Digital Manometer |
Gives better readings and connects to HVAC systems for real-time monitoring. |
Manometer |
Pitot Tube |
Good for measuring flow speed in ducts. Use it with Bernoulli's equation to find the CFM. |
To find the CFM, use this formula when you know the wind speed (Velocity) and vent area (Area):
CFM = Wind Velocity (FPM) x Vent Area (sq. ft.)
Where FPM (Feet Per Minute) measures wind speed, vent area is in square feet. For example, if the wind speed is 500 FPM and the vent area is 2 square feet:
CFM = 500 x 2 = 1000 CFM.
A Pitot tube measures pressure difference. You can use the Bernoulli equation to find wind speed. Then, calculate the CFM.
Wind speed (FPM) = 1096 x √ΔP
where ΔP is the pressure difference in inches of water column.
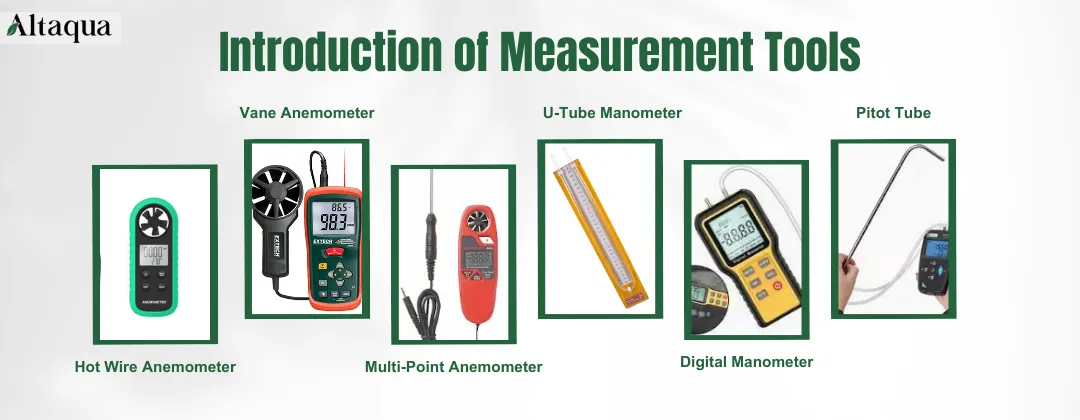
Common Measurement Mistakes and Correct Measurement Methods
When measuring CFMs, common mistakes can cause data errors. These errors can impact HVAC system commissioning and optimization. Here are the common mistakes and how to measure correctly.
1. Single-point measurement leads to too much error.
Mistake: Measurement occurs at just one point in the air outlet or duct. This ignores the uneven air velocity distribution.
Possible consequences: Measurement error could go over 25%. This leads to wrong air volume calculations. As a result, it can impact equipment commissioning and load assessment.
Correct method: Use the nine-point grid method (3×3 measurement matrix) to check air velocity. Measure at several points in the air outlet or duct. Then, average the values for more accurate airflow data.
2. Neglecting air density changes, resulting in measurement inaccuracy at high altitudes
Mistake: Use standard air density to calculate CFM at high altitude without considering the effect of air pressure on air density.
Possible consequences: Lower air density can change the CFM calculation. This may affect airflow regulation and how we evaluate equipment performance.
Correct method: Use the real-time air pressure value in the formula. Adjust it based on local air density. This ensures accurate CFM calculation.
3. Probe blocking leads to inflated wind speed reading
Incorrect practice: The anemometer probe isn’t fully exposed to airflow during measurement. If the angle isn’t right, it can block airflow. This leads to inaccurate high wind speed readings.
Possible consequence: Wind speed could be overestimated by 30-50%. This may lead to a CFM calculation that is much higher than the real airflow.
Correct method: Hold the anemometer probe straight up to the airflow. Make sure your hand or other objects do not block it. This way, you'll get accurate wind speed data.
4. Failure to calibrate the measuring tool regularly, resulting in an increase in the cumulative error.
Avoid using uncalibrated anemometers or manometers for long periods. They need regular testing and calibration.
Possible consequences: The equipment's cumulative error could hit 15%. This impacts CFM calculations and leads to inaccurate commissioning data for HVAC equipment.
Check and adjust measuring tools each month. Use a calibrated wind tunnel or standard airflow test equipment. This ensures accuracy and consistency.
In addition to manual calculations, you can also use the power of an online calculator.
Type of error |
Result |
Proper Method |
---|---|---|
Single-point measurement |
Error > 25 |
Nine-point grid method (3 × 3 measurement matrix) |
Ignore air density |
High altitude CFM calculation inaccuracy |
Insert real-time air pressure values into the formula |
Probe occlusion |
The wind speed reading is 30%-50% higher |
Keep the probe perpendicular to the airflow |
Uncalibrated tool |
Cumulative error of up to 15 |
Verify once a month using a calibrated wind tunnel |
When Do You Need a CFM HVAC Diagnosis?
HVAC issues in the grow room, like duct condensation or fast compressor cycling, often show there are airflow (CFM) problems. So, a professional diagnosis is necessary.
Pipe Condensation
Duct condensation is a common issue. You may see water droplets or dripping on the ducts' outside or inside. This leads to dampness on ceilings and walls, which can even harm equipment. The main cause is low wind speed. This traps wet air inside the ducts, so condensation can't be removed quickly by airflow.
Also, poorly designed pipe sizes, whether too large or too small, can disrupt air volume and block airflow. When the supply air temperature is too low, the duct surface can drop below the air's dew point. This can lead to increased condensation.
To solve these problems, we need to lower the risk of condensation. We can do this by adjusting the CFM. This will help ensure that air moves quickly enough to limit moisture build-up.
Next, we should optimize duct design. This means picking the right duct sizes and using good insulation materials.
Also, raising the supply air temperature can help avoid low duct surface temperatures. Combining this with a separate dehumidification system will cut down air humidity. Together, these steps will help prevent condensation.
Compressor Short Cycling
Another situation needing CFM diagnostics is compressor short cycling. This happens when the compressor starts and stops often, running for too short a time. This leads to higher energy use and more wear on the equipment.
A key cause of this issue is insufficient airflow. When airflow is low, the evaporator can't transfer heat well. This prevents the refrigerant from absorbing enough heat, raising the pressure on the high side. As a result, the compressor shuts down frequently.
If the air volume isn't evenly distributed, some areas may have too much or too little wind speed. This imbalance affects the overall load and disrupts the compressor's normal operation.
To solve these problems, optimize airflow settings. This helps the evaporator get enough airflow, which boosts heat transfer efficiency. Also, using a variable-speed fan (EC fan) lets you adjust airflow based on system load. This prevents CFM from being too high or too low, keeping the system running well.
CFM HVAC Optimization Methods for Different Budget Scenarios
CFM optimization affects air flow, humidity control, and energy efficiency in HVAC designs for grow rooms. Budget levels affect the choice of optimization methods. For low costs, basic improvements are used. For higher investments, intelligent solutions are preferred. Each strategy has its own applicable scenarios and advantages.
Low-Cost Optimization
For budget grow rooms, optimizing CFM relies on simple maintenance and small upgrades. These measures are cheap. If done right, they can boost air flow and save energy.
Comparative Analysis of Duct Sealing Methods
Duct leaks often cause CFM loss. Even small leaks can hurt the HVAC system's efficiency. There are three main methods of sealing ducts: aluminum foil tape, glue sealing, and spray sealing.
Aluminum foil tape is the cheapest option. It's good for fixing small duct joints, but it lacks durability. Glue sealing works well for bigger cracks. It offers stronger sealing. However, it can be tricky to apply. Spray sealing technology is suitable for comprehensively optimizing duct sealing. It can penetrate small cracks and reduce air flow loss, but it is relatively expensive.
Air Filter Selection Guide
Air filters can greatly affect CFM, but their importance is often ignored. Choosing the wrong filter can block airflow or lower air quality. For low budgets, choose reusable washable filters. They help cut long-term replacement costs. If the growing room is dusty, choose a MERV 8 filter. It offers basic air purification and maintains good airflow. For rooms that need good air quality, pick a high-efficiency filter with a MERV rating of 11 to 13. Just make sure the fan can handle the extra air resistance.
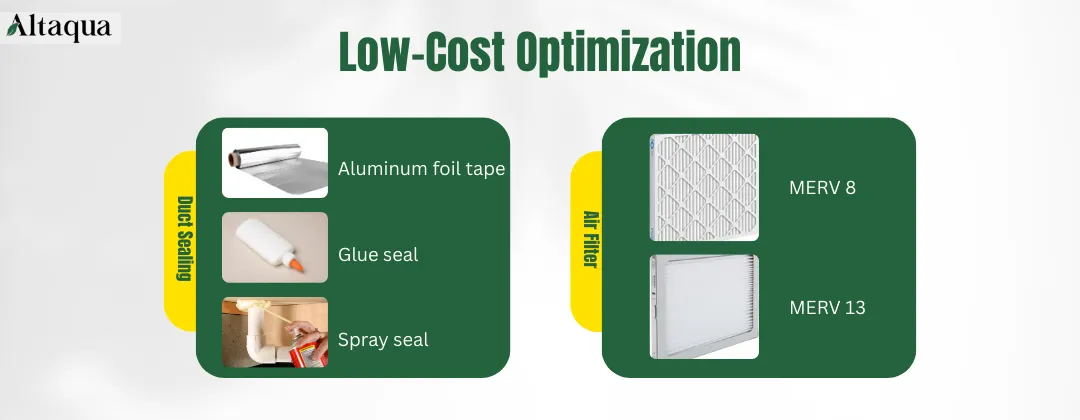
Air Flow Optimization for Medium Budgets
When the budget allows, think about adding better aerodynamic systems. Use ECM motors and zoning control systems. They can boost CFM adaptability and save energy.
Energy Efficiency of ECM HVAC Motors and Application Scenarios
ECM (electronically commutated motor) fans change wind speed based on the needs of the cultivation room. This makes them more energy-efficient than traditional PSC (permanent magnet motor) fans. They also provide precise control over CFM. ECM motors are very efficient, even at low speeds. This makes them great for cultivation rooms where humidity changes a lot.
At night, when humidity is high and cooling needs are low, ECM motors can lower air volume. This helps maintain humidity control without any loss. Also, you can adjust the ECM motor from a distance using the controller. This boosts the system’s flexibility.
Partition Control Systems
Partition control systems can adjust the CFM for each space. They do this based on the temperature and humidity needs of different areas in the growing room. This improves air circulation accuracy. In a facility with various growth stages, the seedling area needs less CFM. This helps keep a stable temperature. In contrast, the flowering area needs more CFM to manage humidity.
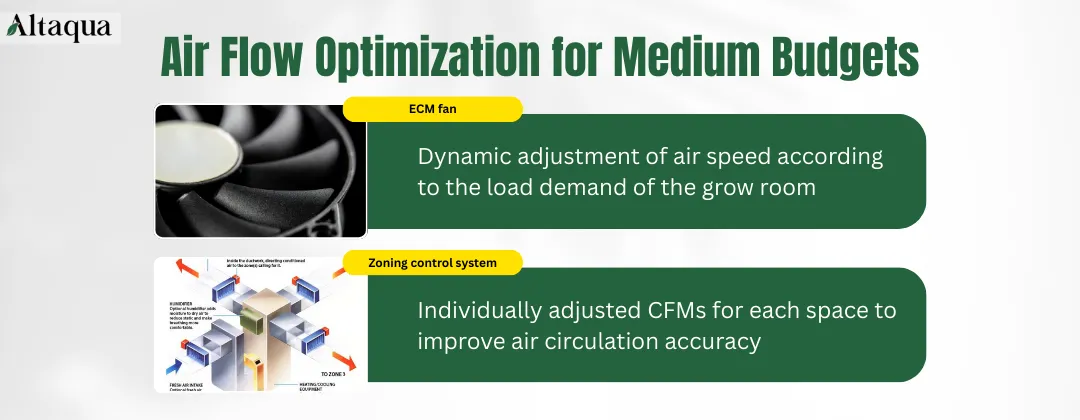
Comprehensive Optimization Solutions for High Inputs
Advanced HVAC designs boost energy efficiency and control in grow rooms. Using fresh air systems and AI-driven CFM control boosts operations and plant quality.
The Role of Independent Fresh Air Systems in Humidity Control
Independent fresh air systems can manage air exchange volumes on their own. They do not depend on the main HVAC plant. This allows for better management of humidity levels. Traditional grow room HVAC mainly uses air conditioning or dehumidifiers to manage humidity. However, independent fresh air systems can help.
They regulate the humidity and temperature of outside air. This approach reduces the need for mechanical dehumidification and lowers energy use. In a humid place, bringing in dry outside air can lower indoor humidity. In winter, a heat recovery fresh air system helps save heat and keeps air quality steady.
Prospects for Artificial Intelligence-Regulated CFM HVAC
AI control systems are becoming the future of HVAC optimization in grow rooms. AI uses sensors to track important factors such as temperature, humidity, and VPD (vapor pressure difference) in real time. It can then adjust CFM automatically to meet the current environmental needs. When light intensity changes, the AI system can boost CFM to cool down more.
At night, it lowers wind speed to save energy. Future HVAC systems will use advanced AI algorithms. They will predict environmental changes and optimize automatically. This will boost cultivation efficiency and extend equipment lifespan.
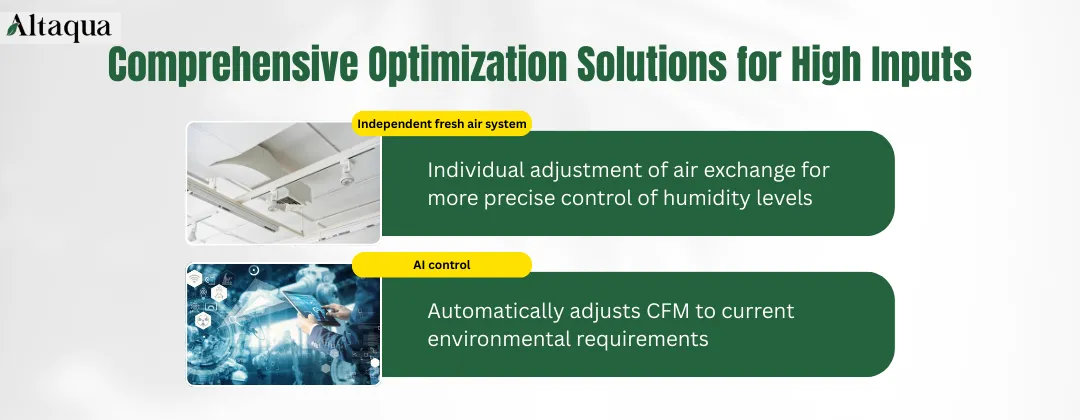
Altaqua Grow Room HVAC System – A Comprehensive and Advanced Solution
Altaqua Grow Room HVAC System is made for grow rooms. It features a smart CFM control solution. This ensures good air circulation, manages humidity well, and saves energy.
Integrated Ductwork and Airflow Optimization
Altaqua's modular duct design helps spread air evenly. This way, it prevents “dead spots” and reduces areas with high humidity in the growing room. The air volume of the system is precisely calculated to optimize CFM and reduce energy loss.
Efficiency and Performance of EBM EC Fans in CFM Control
Altaqua Grow Room HVAC System uses EC fans from the EBM brand. The pressure sensor helps adjust the fan speed based on the return air temperature. Compared with traditional fans, it can save 30-50% of energy. EC fans cut wind noise, boost system stability, and make crop management easier.
Independent Fresh Air and Exhaust Air System for Precise CO₂ Management
Altaqua Grow Room HVAC System has a fresh air and exhaust air system. This system can accurately control the indoor CO₂ levels. It can be managed manually or automatically. When CO₂ levels drop below 400 PPM, the CO₂ generator turns on. It stops once it reaches the target level. If CO₂ levels go over 1000 PPM, the fresh air and exhaust systems will turn on automatically. Monitoring air quality in real time keeps cannabis growing in the best environment. The independent exhaust air system takes away extra moisture, stops mould from growing, and helps air circulate better.
Heat Recovery Dehumidification for Energy-Saving Moisture Control
Altaqua Grow Room HVAC System features an advanced heat recovery design that captures waste heat from the cooling process and repurposes it to reheat dehumidified air before returning it to the grow room. This process prevents excessive cooling, stabilizes the environment, and reduces the need for additional heating. By maintaining consistent temperature and humidity levels, the hvac for grow rooms enhances energy efficiency and creates optimal conditions for plant growth.

Advantages and Disadvantages of Different CFM HVAV Choices
CFM, or cubic feet per minute, is key for air circulation in growing facilities. A high CFM boosts airflow, but it’s not always best. Similarly, a low CFM works for specific situations. Choosing the right CFM affects temperature, humidity, energy use, noise, air quality, and crop growth.
Discussion on Whether High CFM HVAC is Always Better
Does a higher CFM mean better? A high CFM means faster air exchange. This helps keep temperature and humidity steady. It also reduces CO₂ and moisture build-up. But sometimes, a high CFM can lead to more energy use, increased noise, and harm to crop growth.
The Relationship Between Noise and Energy Efficiency in Grow Rooms
A high CFM generally means a higher fan power, which may result in a higher noise level in the growing room. Long hours in the growing room can be tough. High noise levels reduce comfort and can hide important sounds, like equipment alarms. Also, very high wind speeds can cause air turbulence. This may affect how stable temperature and humidity sensors are. Generally, 300 to 400 CFM per minute per ton of capacity is recommended.
Impact of Duct Design on High CFM HVAC Operation in Cultivation Facilities
The effectiveness of high CFM relies on duct design. If ducts have too many elbows, small diameters, or leaks, raising CFM may not help air circulation. Instead, it can strain the fans and lower energy efficiency. In large growing facilities, poor air delivery can lead to too much ventilation in some areas and not enough in others. This can harm the overall environment uniformity.
Industry Scenarios Where Low CFM HVAC is Applicable
Low CFMs are better in some growing environments, even with high CFM benefits. In tight grow rooms, VPD-optimized setups, and multi-story vertical systems, low CFM helps keep a stable environment. It does this by improving airflow management.
Demand for Low CFM HVAC in Sealed Cannabis Grow Rooms
In a sealed grow room, air circulation depends on controlling the internal system instead of using outside air. A high CFM can make humidity control unstable and use more energy. Lowering the CFM helps air move slowly and evenly. This way, temperature and humidity sensors can better detect changes. It also reduces CO₂ and humidity swings, creating a more stable environment for the plants.
Application of Low CFM HVAC in VPD-Optimized Grow Environments
VPD impacts plant transpiration. High CFM can speed up water evaporation from leaves, causing water management issues. By keeping CFM low, air spreads evenly among plants. This helps avoid strong winds that can disrupt VPD. A low CFM helps control humidity. It balances how much water plants take in and give off.
Low CFM HVAC in Multi-Tier Vertical Farming and Its Effects on Microclimates
In multi-layer vertical farming, a high CFM can lead to large temperature and humidity shifts between layers. This can hurt crop growth. By lowering the CFM and using directional airflow, we can reduce turbulence. This helps distribute air evenly, preventing some leaves from drying out or becoming too humid. Also, a lower CFM uses less energy and keeps CO₂ levels stable.
Frequently Asked Questions in CFM HVAC Operation
Improper CFMs in grow room HVAC can cause problems. You might see uneven airflow, evaporator icing, and inconsistent CO₂ levels. It’s important to understand these problems. Adjusting the CFM for various growing needs can boost air quality and crop uniformity.
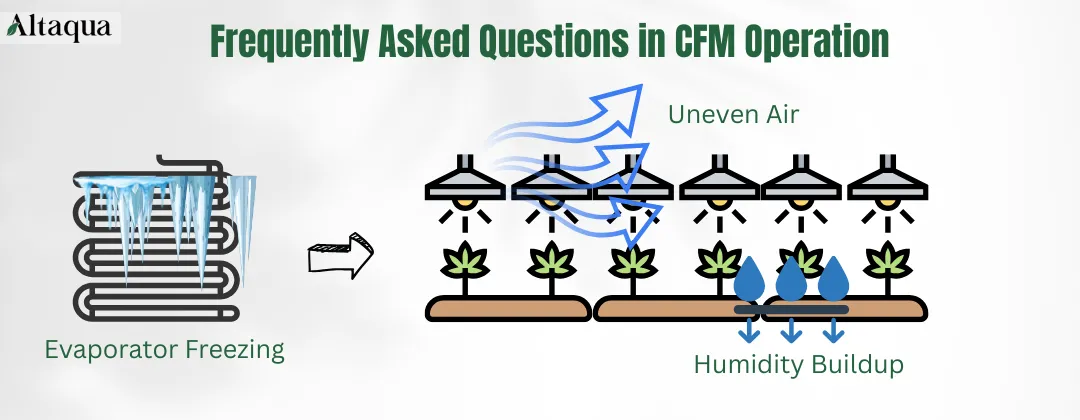
Underperforming Airflow Due to Incorrect CFM HVAC Settings in Grow Rooms
If the CFM settings are too low, grow rooms can have poor airflow. This leads to high humidity, which increases the risk of mold and disease. Also, CO₂ may not spread well, hurting the plants' ability to photosynthesize.
But if the CFM is too high, air moves too quickly. This can lower humidity on leaf surfaces and speed up water evaporation. It might even cause stomata to close, which affects nutrient absorption.
It's important to adjust the CFM. Consider the planting area, plant growth stage, and environmental needs.
Relationship Between Evaporator Icing and CFM HVAC in Dehumidification Systems
In a dehumidification system, low CFM can mean poor air flow to the evaporator. This can make its temperature drop below freezing, leading to icing. When the evaporator freezes, it lowers the system's dehumidification capacity. This also raises energy use and can destabilize the HVAC equipment. To prevent these issues, increase the CFM and optimize fan operation. This ensures the dehumidification system runs smoothly in various humidity conditions.
How CFM HVAC Affects CO₂ Distribution and Plant Growth Uniformity
The effect of CFM on CO₂ distribution is important. In a CO₂ delivery system, low CFM makes it hard to spread CO₂ evenly. This leads to high CO₂ levels in some spots and low levels in others, hurting photosynthesis. On the other hand, high CFM can dilute CO₂ too fast, wasting its use. So, it’s essential to find the right CFM during CO₂ application. This method helps air circulate evenly. It spreads CO₂ well, without excessive dilution. This boosts plant photosynthesis.
Conclusion
The selection and optimization of CFM is critical to managing air circulation in the growing room. A high CFM can boost air movement and lower moisture. However, it might also raise noise, use more energy, and impact system efficiency. But if the CFM is too low, it can cause uneven temperature and humidity. This may harm photosynthesis and transpiration in crops. It might even lead to diseases. When choosing CFM, growers should consider the growing space. They also need to think about how air moves and their energy efficiency goals. This helps achieve the best balance.
CFM optimization solutions for different budgets provide flexible options. Growers on a budget can boost air circulation by sealing ducts well and choosing the right air filter. Medium-budget solutions can upgrade ECM fans to boost energy efficiency. They can also add a zoning control system for better environmental regulation. High-investment cultivation facilities benefit from advanced solutions. These include independent fresh air systems, AI CFM regulation, and heat recovery dehumidification. They help control the environment more efficiently. This optimizes air quality and reduces energy use in the cultivation room.
No matter which optimization solution you pick, it’s important to set the CFM correctly. Avoiding common measurement mistakes also helps improve cultivation efficiency and crop quality. With scientific CFM management, growers boost energy efficiency. This creates a stable and healthy cultivation environment. As a result, they achieve higher yields and better quality crops.
FAQ
1. What is CFM HVAC and what is its role in the HVAC system of the cultivation room?
CFM (Cubic Feet per Minute) is a key indicator of air circulation and is crucial in the design of the cultivation room HVAC. CFM HVAC directly affects temperature and humidity control, air quality and CO₂ distribution. A low CFM HVAC can cause moisture buildup, leading to mould and disease. On the other hand, a high CFM can raise energy use and disrupt air flow. When designing the HVAC system for the growing room, calculate the CFM HVAC carefully. It’s based on the room size, heat load from equipment, and dehumidification needs. This ensures a stable environment for the crops and efficient energy use.
2. How do I calculate the CFM required for the HVAC system in the growing room?
To calculate CFM, you need to think about the space size, heat load, humidity control needs, and ventilation method. A basic formula for CFM is CFM = (room volume × air changes per hour) / 60. The air changes per hour vary based on the crop type and humidity needs. A closed grow room needs a higher air change rate. This helps keep the VPD (vapor pressure difference) at the right level. Also, it should be adjusted based on actual use, following ASHRAE and EPA guidelines. This will help ensure even air movement and prevent hot and cold spots.
3. Is a high CFM always better in the HVAC system of the growing room?
Not really. A higher CFM HVAC boosts air flow and cuts moisture. But, it can also raise noise, lower energy efficiency, and cause uneven temperature and humidity. Also, a high CFM HVAC can cause very high wind speeds if the duct design isn’t good. This can affect crop transpiration and lower CO₂ use. Therefore, the CFM HVAC in the growing room should be set reasonably according to specific needs. You can control airflow better by optimizing the duct layout and using variable-speed fans (EC fans). Don't just chase higher CFM.
4. How can CFM HVAC be optimized to improve the energy efficiency of the HVAC in the growing room?
Optimizing CFM HVAC requires a comprehensive consideration of budget and growing needs. Low-cost optimization methods are sealing ducts and choosing the right air filter. These steps help cut down on air leakage and wind resistance. Medium-budget choices feature ECM HVA Cmotors. They adjust air speed based on demand, boosting energy efficiency. High-investment options include a standalone fresh air system, intelligent CFM HVAC adjustment technology, and a heat recovery dehumidification system, which can precisely control humidity while reducing energy consumption. Optimizing CFM HVAC helps growers enhance HVAC efficiency. This ensures crops thrive in the best environment and lowers long-term costs.
Share with your friends:
Popular Blogs on Altaqua:
Download Catalogue