Why Cannabis HVAC Is Essential for Optimal Cultivation Results (Update)
When growing high-quality cannabis, maintaining the perfect environment is crucial. This is where cannabis HVAC systems come into play. They not only regulate the temperature, but also create the ideal conditions for the plants to thrive, ensuring that every growth stage is optimized for success.
Growing cannabis indoors requires precision control. Temperature, humidity, airflow and carbon dioxide levels all need to be balanced to mimic the plant's natural environment. Without a reliable cannabis HVAC system, controlling these factors can be an unpredictable challenge. That's why more and more growers are turning to integrated solutions to ensure everything is in sync for healthier plants and a more efficient growing process. This article explores how cannabis HVAC systems can improve growing efficiency, enhance plant vitality and help you achieve optimum results.
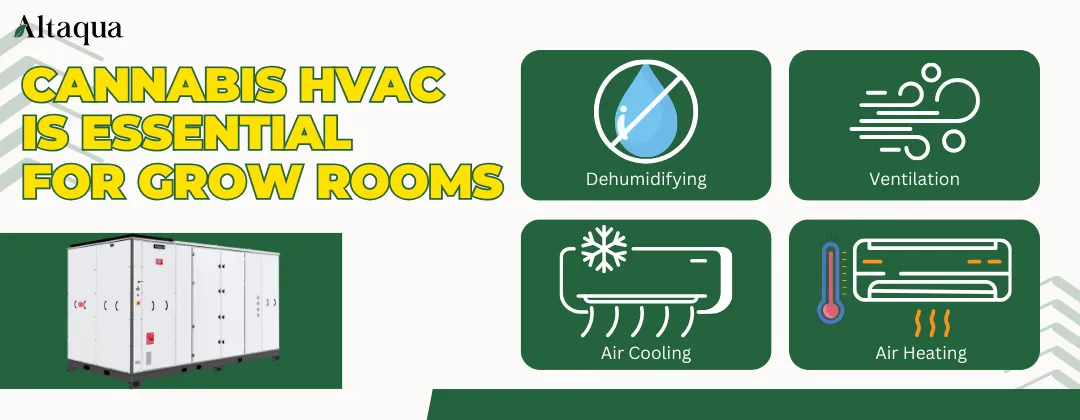
Why Cannabis HVAC Is Crucial for Cannabis Cultivation
The health of the cannabis plant is directly affected by the growing environment. A well-designed cannabis HVAC system helps maintain a stable environment. Without a reliable cannabis HVAC system, managing the ever-changing environmental conditions in the grow room will be an ongoing challenge.
Cannabis HVAC Effects on Cannabis Health
Cannabis is extremely sensitive to changes in temperature, humidity and airflow. Even small fluctuations in temperature or humidity can cause stress, resulting in slow growth or poor crop quality. Cannabis HVAC systems are designed to meet the unique needs of cannabis cultivation. Cannabis HVAC provides precise control of a variety of environmental factors to create the optimum growing environment, supporting healthy growth and boosting yields.
Impact on Plant Growth Rate
Cannabis grows best when environmental conditions are ideal. Temperature and humidity affect the speed and efficiency of photosynthesis, which in turn affects the growth rate. Cannabis HVAC systems precisely control temperature and humidity to maintain an ideal range of levels.
For example, if the room is too hot or cold, or the humidity is too high or too low, the cannabis will be stressed, which slows down growth. A cannabis HVAC system helps to prevent these problems by constantly monitoring and regulating temperature and humidity to maintain the optimum growth range and help the cannabis grow at the ideal rate.
Prevention of Diseases and Pests
Fluctuating humidity and temperature provide the perfect breeding ground for pests and diseases, which can quickly destroy a crop. A proper cannabis HVAC system helps prevent these problems by maintaining a stable and controlled environment. Constantly regulated temperature and humidity levels make it harder for pests such as mould, mildew and spider mites to thrive. By preventing problems before they arise, cannabis HVAC systems help plants to be healthier and reduce the need for chemical intervention.
Cannabis HVAC Compatibility with Other Systems
Growing cannabis usually involves multiple systems working together. Cannabis HVAC does not operate in isolation; it needs to communicate and collaborate with other important systems, such as irrigation, environmental control and even lighting. Therefore, when purchasing cannabis HVAC, growers should pay attention to whether it is compatible with the rest of the systems in the grow room.
Integration with Automated Irrigation Systems
One of the key advantages of cannabis HVAC systems is their ability to integrate with automatic irrigation systems. While an automated irrigation system regulates the amount of water supplied to the cannabis, the HVAC system ensures that the humidity level in the grow room is maintained at the ideal range. This integration helps prevent overwatering or underwatering, both of which can have a negative effect on the growth of the cannabis.
With the right system, growers don't have to worry about the fluctuations in humidity that can result from manual watering. Together, the HVAC system and the irrigation system will work to maintain a stable grow room environment that is conducive to healthy cannabis growth.
Communication with Environmental Control Systems
The Cannabis HVAC system also works best when integrated with other environmental control systems. These may include CO₂ controllers, lighting systems, and even air filtration units. Cannabis HVAC can communicate with these systems to help keep all environmental factors in line. For example, if the temperature in the grow room increases due to increased light or CO₂, the HVAC system can adjust accordingly to keep the room temperature at the optimal level for cannabis growth.
Cannabis HVAC Versus Decoupled HVAC
When selecting the right climate control solution for your cannabis grow room, it is important to understand the difference between an integrated cannabis HVAC system and Decoupled HVAC system. Decoupled HVAC systems typically consist of individual units such as air conditioners, dehumidifiers and chillers, and are used in many industries. However, for cannabis cultivation, an integrated cannabis HVAC system offers many advantages, particularly in terms of efficiency, performance and long-term cost savings.
Cannabis HVAC vs. Air Conditioner+Dehumidifier
The combination of an air conditioner and dehumidifier is one of the most common setups for controlling a variety of environmental temperatures and humidity levels. While these two systems can help cannabis maintain a comfortable climate, they often fall short of the precision and integration needed for optimal health and yield.
Efficiency and Performance Comparison
In terms of efficiency, Cannabis HVAC systems outperform air conditioning + dehumidifier setups in several key areas. Air conditioners and dehumidifiers are designed to operate independently, which means they often require more energy to maintain the desired environment. For example, when an air conditioner cools the air, it also inadvertently lowers the humidity level. When a dehumidifier is running, it also releases heat, increasing the load on the air conditioner to cool. In contrast, Cannabis HVAC systems are designed to handle both temperature and humidity, using integrated controls. This not only saves on energy costs, but also ensures that the environment remains stable without excessive fluctuations.
Cost Implications for Installation and Operation
From a cost perspective, while the initial investment in a Cannabis HVAC system may be higher than installing an air conditioner and dehumidifier separately, in the long term, the costs will be significantly lower. This is because the integrated efficiency of the Cannabis HVAC system reduces the need for frequent maintenance and energy-consuming adjustments. Over time, this will reduce operating costs.
On the other hand, the air conditioning + dehumidifier combination can lead to increased maintenance and operating costs. These systems require constant monitoring and adjustment to prevent conflicts between temperature and humidity, and they often require a separate power supply, which can increase electricity costs.
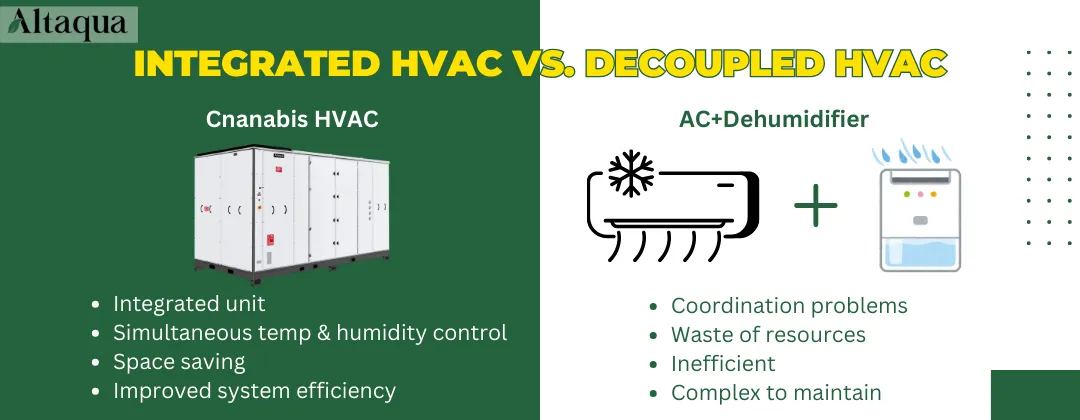
Cannabis HVAC vs. Chiller+AHU
Another setup commonly used in larger facilities is a combination of a chiller and an air handling unit (AHU). While these systems can effectively manage cooling and airflow, they are somewhat complex and less suitable for smaller or more precise applications, such as cannabis cultivation.
System Complexity and Maintenance
Chiller + AHU systems are highly complex and often involve multiple units that need to be carefully coordinated to maintain proper environmental conditions. This complexity can lead to more frequent maintenance and troubleshooting, as the different components may not always work seamlessly together. The challenge with these systems is that they were originally designed for large industrial applications and may not provide the same level of precise temperature and humidity control that Cannabis HVAC systems can offer.
In contrast, Cannabis HVAC systems are designed with cannabis cultivation in mind. They integrate all aspects of climate control into one system, making them easier to maintain. This not only simplifies setup, but also troubleshooting, ensuring smooth system operation over the long term.
Energy Consumption and Cost Efficiency
Cannabis HVAC systems are generally more energy efficient than chiller + AHU systems in terms of energy consumption. Chillers and AHUs typically consume more electricity, especially in environments that require constant adjustment of cooling and airflow. This increase in energy requirements can lead to higher operating costs over the life cycle of the system.
Cannabis HVAC systems, on the other hand, are specifically optimized to minimize energy consumption while maintaining precise climate control. With features such as intelligent humidity control and integrated VPD monitoring, Cannabis HVAC systems adapt in real time to the needs of the grow room, ensuring the ideal environment for cannabis while minimizing energy consumption.
Key Considerations for Cannabis HVAC Design
When designing a cannabis HVAC system, there are several key considerations beyond temperature and humidity control. Let's focus on three areas: environmental control, lighting, and irrigation coordination.
Environmental Control
Environmental control is at the heart of any cannabis grow room. A cannabis HVAC system helps manage the three main elements required for cannabis plants to thrive: temperature, humidity and airflow. These elements must be precisely balanced, as even slight fluctuations can affect plant growth and overall yield.
Temperature and Humidity Regulation
The temperature and humidity requirements for growing cannabis are complementary. The ideal temperature for cannabis varies depending on the growth stage, but is usually 71-82°F (22-28°C) with lights on / 64-75°F (17-23°C) with lights off during vegetative growth, and slightly lower 68-79°F (20-26°C) with lights on / 59-70°F (15-21°C) with lights off. Maintaining a consistent humidity level is also crucial, especially during the flowering stage, as high humidity can lead to mold and mildew problems.
An integrated HVAC system for cannabis can lower both temperature and humidity to provide the optimum environment without excessive energy or equipment use. This intelligent climate control is particularly important in grow rooms, as any instability in the environment can stress the plants and reduce overall health and productivity.
Airflow Management
Cannabis needs a constant flow of air to grow healthily. Lack of airflow can lead to stunted growth and increase the risk of fungal infestation. A good HVAC system circulates air evenly, ensuring that each plant receives a consistent supply of carbon dioxide, which is essential for photosynthesis. Air circulation also prevents hot spots from forming in the grow room and ensures that the entire space is evenly ventilated.
Many cannabis HVAC systems are equipped with variable-speed fans that adjust airflow based on the temperature and humidity in the room. This automatic adjustment ensures that the system operates efficiently, without overloading or wasting energy. It benefits plant growth and saves costs.
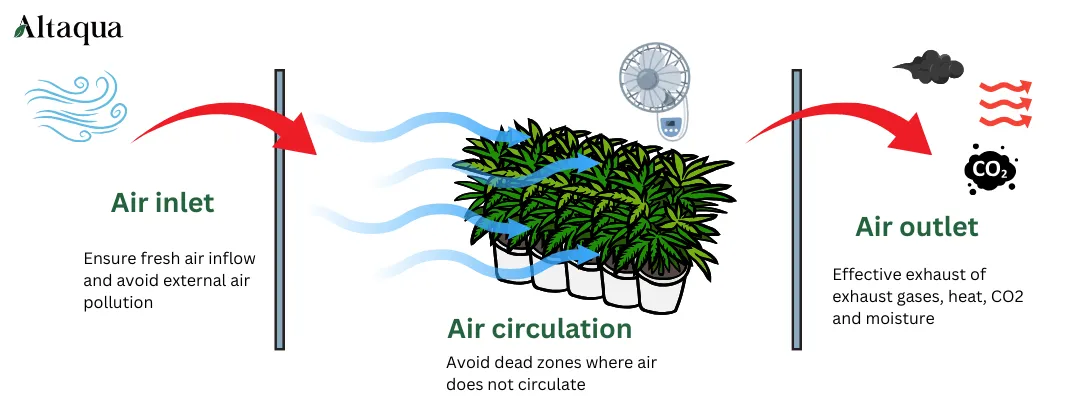
CO₂ Concentration Control
Cannabis also needs a stable carbon dioxide concentration (CO₂) to grow effectively. While the natural CO₂ concentration in the atmosphere is sufficient for most plants, cannabis plants benefit from high CO₂ concentrations, especially during the growth phase. A cannabis HVAC system can help maintain an optimal CO₂ concentration, promoting growth and increasing yield.
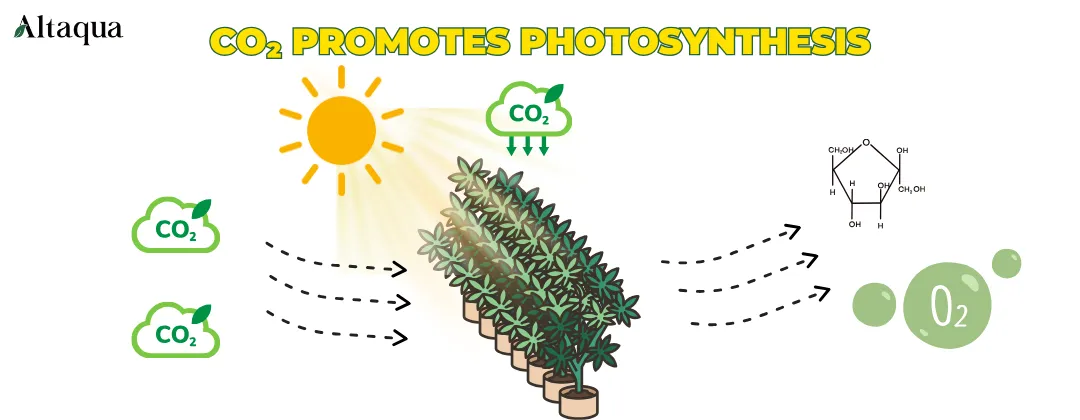
Lighting and Irrigation
Both lighting and irrigation affect temperature, humidity and the overall health of the cannabis. A good cannabis HVAC system not only manages the indoor climate, but also integrates perfectly with the lighting and irrigation systems.
Heat Load Management for Lighting
Lighting is an integral part of cannabis cultivation, but it also generates heat, and overheating can damage the plants and disrupt the growing environment. Many modern cannabis HVAC systems are designed to handle the heat load generated by grow lights, ensuring that they can operate efficiently without overheating the room. By adjusting airflow and cooling capacity according to the number and intensity of the lights, cannabis HVAC systems can maintain a constant temperature.
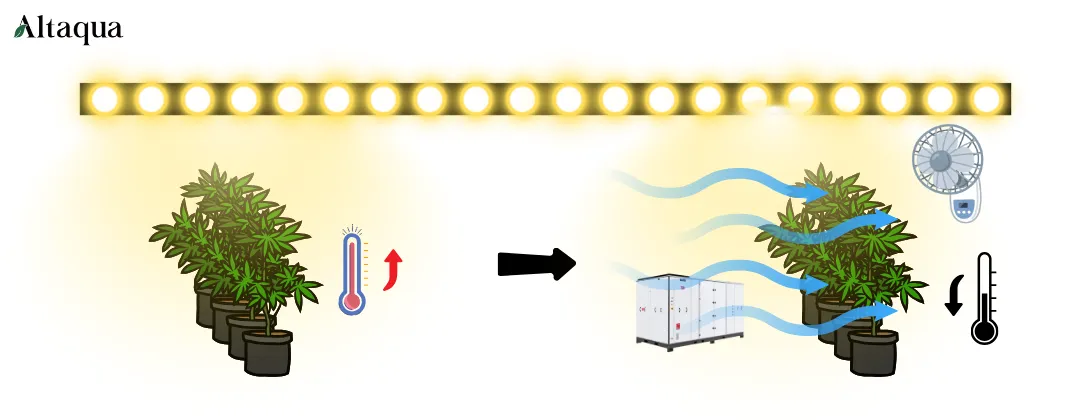
Humidity Impact from Irrigation
Irrigation is another factor that directly influences the humidity level in the grow room. Over-irrigation or an inefficient irrigation system can lead to excess humidity, creating conditions for mold and fungal growth. Cannabis HVAC systems that are integrated with the irrigation system can automatically regulate humidity according to the watering schedule to alleviate these problems. Precise humidity control minimizes the risk of fungal infections.
Integrated Water and Nutrient Management
One of the most innovative features of modern cannabis HVAC systems is their ability to integrate with moisture and nutrient management. By coordinating HVAC functions with irrigation and fertilization systems, these integrated systems seamlessly optimize cannabis growing conditions.
Coordination of Humidity and Irrigation
In many grow rooms, managing humidity and irrigation requires constant attention. However, cannabis HVAC systems can simplify this process by adjusting both humidity and watering schedules simultaneously. This integrated approach ensures that cannabis receives the right amount of moisture without causing humidity imbalances.
Condensate Recovery and Utilization
Condensate recovery is another important function of the Cannabis HVAC system. Condensate is naturally produced when the Cannabis HVAC system cools the air. Modern HVAC systems don't let this water go to waste, but collect it and recycle it, reducing water consumption and supporting sustainable cultivation. The recovered water can be injected into the irrigation system, making effective use of excess moisture and reducing the need for additional water sources.
According to a case study on condensate water recovery at the GSA Metcalf Federal Building in Chicago, the building saved more than 150,000 gallons of water in one year by collecting the condensate water from the cooling system, which provides about 15% of the water demand for the cooling tower, and reduces the amount of water entering the Chicago Sanitary and Combined Sewer System.
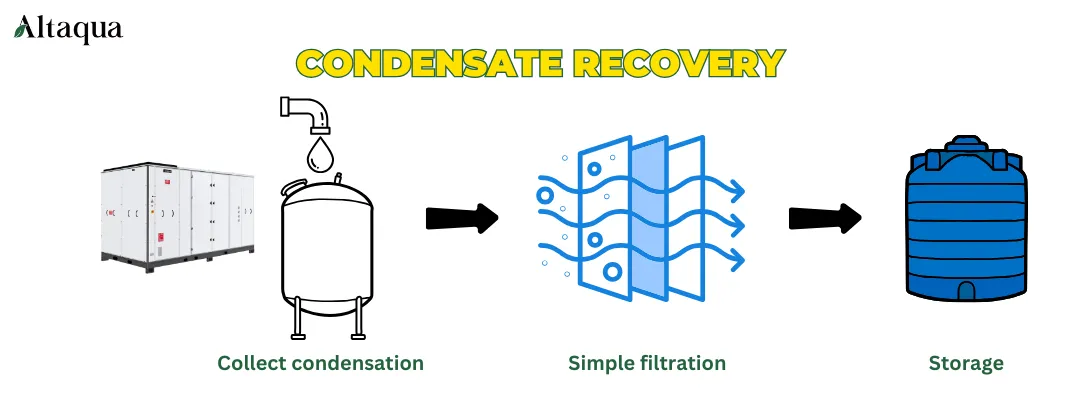
Nutrient Delivery Efficiency
Finally, the integration of Cannabis HVAC with the nutrient delivery system ensures that cannabis receives the right nutrients at the right time. This reduces nutrient waste, improves efficiency and contributes to the overall health of the cannabis. By synchronizing temperature, humidity, carbon dioxide and nutrient levels, the Cannabis HVAC system helps cannabis absorb nutrients more efficiently, promoting faster growth and higher yields.
Component Selection for Cannabis HVAC
The components of a cannabis HVAC system directly determine its performance, efficiency and durability. Because cannabis cultivation requires a tightly controlled environment, the selection of HVAC components must be tailored to the unique needs of the grow room.
Component Durability and Long Lifespan
One of the most important factors when selecting HVAC components is durability. Cannabis HVAC systems typically need to operate continuously around the clock to maintain the right conditions in the grow room. Due to continuous use, components can wear out quickly, leading to expensive repairs and downtime. To prevent this, it is crucial to select components that are built to last.
For example, Altaqua Grow Room HVAC System features high-quality compressors from Danfoss and Panasonic and EC fans from EBM designed to withstand the constant operation required in cannabis facilities. These components need to withstand the stress of long hours of operation, often in high humidity, without deteriorating or losing efficiency. Investing in durable components ensures that your system will run smoothly for longer, reducing maintenance costs and extending the life of the entire HVAC system. This not only saves money in the long run, but also ensures that your cannabis plants are always in a stable environment, which is essential for optimal growth.
High Precision and Quality of Spare Parts
In the field of cannabis HVAC, precision is crucial. Each component of the cannabis system must be able to perform its specific function accurately. Whether it is a dehumidifier, thermostat or air handler, each component must be able to control temperature, humidity and airflow with high precision. Errors in the system can cause fluctuations in the grow room environment, which can damage the cannabis plants.
High-quality components such as temperature sensors, humidity controllers and pressure valves must maintain their accuracy over time. These components are manufactured to high standards and help the system maintain precise climate control to meet the needs of the cannabis plant. For example, Altaqua Grow Room HVAC System uses high-quality E+E high-precision temperature and humidity probes to prevent temperatures from becoming too high or too low and ensure that the plants are kept within an optimal temperature range. Similarly, advanced humidity sensors ensure that humidity levels remain stable, reducing the risk of mould and other fungal diseases.
Parts are Widely Available
Another key consideration when selecting HVAC components is the availability of spare parts. Growers need to be able to get hold of spare parts quickly when the cannabis system breaks down. Cannabis HVAC systems often rely on a combination of custom-made and off-the-shelf components, and it is important that the spare parts on which the cannabis HVAC relies are easy to find and replace.
There is nothing simpler than selecting HVAC components from reputable, well-known manufacturers. These companies usually offer readily available replacement parts through direct sales or third-party suppliers. For example, many of the components in Altaqua's cannabis HVAC come from internationally renowned brands such as Schneider's electrical components and ABB's frequency converters. When parts are easy to replace, downtime can be minimized and the optimal environment in the grow room can be maintained.
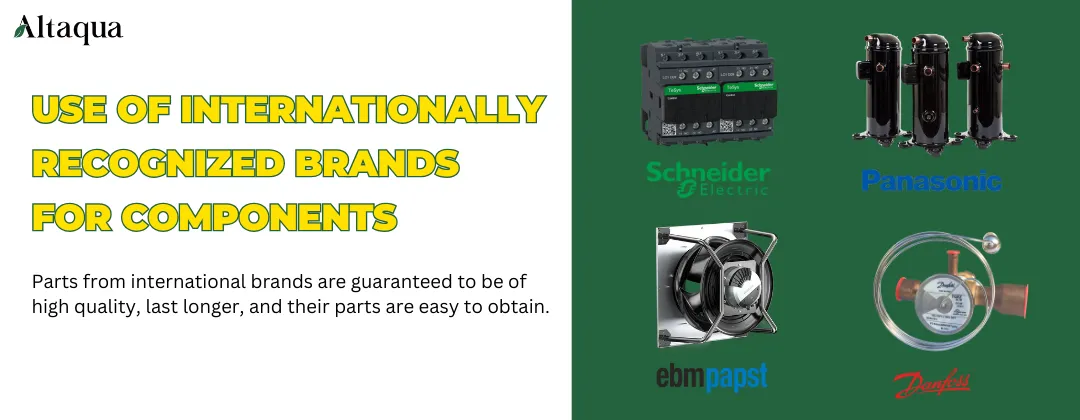
Manufacturing and Testing of Cannabis HVAC System
Manufacturing a cannabis HVAC system involves more than just putting the individual parts together. To ensure that the system is well-suited to cannabis cultivation, manufacturers follow very specific processes and carefully test each unit before it leaves the factory.
A Tightly-controlled Manufacturing Process
Creating a HVAC system for cannabis requires precision and consistency. Every system component, from the compressor to the air handler, is carefully selected, assembled and tested to ensure it meets the specific needs of the cannabis growing environment. At every step of the production process, the system is inspected to ensure it is functioning properly. This attention to detail ensures that the cannabis HVAC system will perform well in your grow room, reducing the risk of failure and creating the best conditions for plant health.
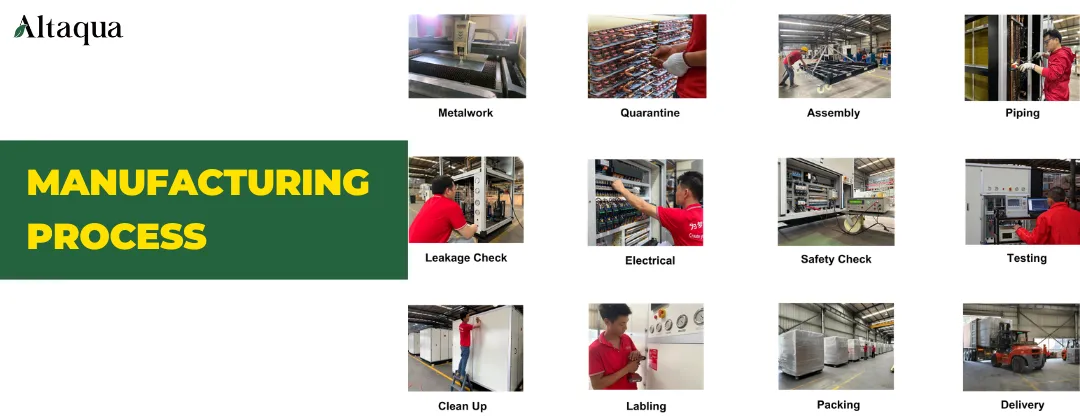
Customization Options for Cannabis HVAC Systems
Every cannabis grow room is unique, so one-size-fits-all approaches don't always work for HVAC systems. Customization services allow you to tailor the system to your specific needs. Many cannabis-specific HVAC manufacturers offer custom solutions to meet the specific needs of grow rooms, whether it's adjusting for room size, unique temperature and humidity requirements, or special considerations like airflow patterns or CO₂ levels. Customization services include sizing the system, airflow, or adding advanced features such as humidity sensors or air filtration systems.
These custom units integrate seamlessly with existing cannabis grow room facilities to ensure optimal environmental conditions for cannabis health and growth. Whether you operate a small home grow or a large commercial grow, customizing the HVAC system to fit your space will make it work better and use less energy.
Every Unit is Factory Tested
Testing is an important step in the manufacturing process of a cannabis HVAC system. Each unit is tested to ensure that all components are working properly and that the system can maintain the precise conditions required for growing cannabis. These tests check the system's ability to regulate temperature, control humidity, manage airflow and maintain stability. Factory testing simulates real-world conditions to ensure that the system can withstand long hours of use in the grow room.
Any potential problems are identified and resolved before the system is shipped, reducing the chance of breakdowns and repairs after installation. By testing each unit before it leaves the factory, the manufacturer ensures that growers receive a product that will perform optimally from day one, reducing the likelihood of system failure or inefficiency.
Transporting Cannabis HVAC Systems
Shipping cannabis HVAC systems involves more than just transporting the system from point A to point B. It requires careful planning, proper packaging and timely delivery to ensure that the system arrives in tip-top condition and is ready to be installed.
Packaging and Handling Best Practices
When shipping cannabis HVAC systems, proper packaging is essential to ensure that all components remain intact and functional throughout the shipping process. Custom crating and padding are commonly used to protect these units, with special attention paid to fragile components that may be susceptible to bumps or rough handling.
As well as protective packaging, clear labelling is also key to proper handling. Each crate or box contains detailed instructions on how to handle and transport the HVAC system. Manufacturers often work closely with logistics providers to ensure that HVAC systems are transported with maximum protection against damage and arrive at their destination ready to be installed immediately.
Logistics Coordination for Timely Delivery
The delivery of a cannabis HVAC system requires careful logistical coordination to ensure that the system arrives on time and in perfect condition. This is because delays in HVAC installation can cause interruptions to the cultivation process, affecting cannabis growth and overall yield.
To avoid delays, manufacturers often work with reliable shipping companies and develop logistics plans that take into account factors such as distance, road conditions and expected weather. Real-time tracking systems are often used to monitor shipments and provide growers with updates on estimated delivery times.
Installation and Services of Cannabis HVAC
Once the cannabis HVAC system arrives, the next key step is installation. As well as installation, ongoing maintenance and support is essential to maintain the long-term performance of the system.
Installation of Cannabis
When installing cannabis HVAC, growers should pay attention not only to whether it is installed correctly, but also to leaving a certain safety distance to facilitate the operation and future maintenance of cannabis HVAC.
Easy-to-operate Installation
Cannabis HVAC systems are straightforward to install and can be easily operated by anyone, even if they are not HVAC experts. Many systems come with detailed manuals and installation videos to ensure that the whole process is as easy as possible. For those who are not familiar with HVAC systems, following the instructions is said to be easy to install.
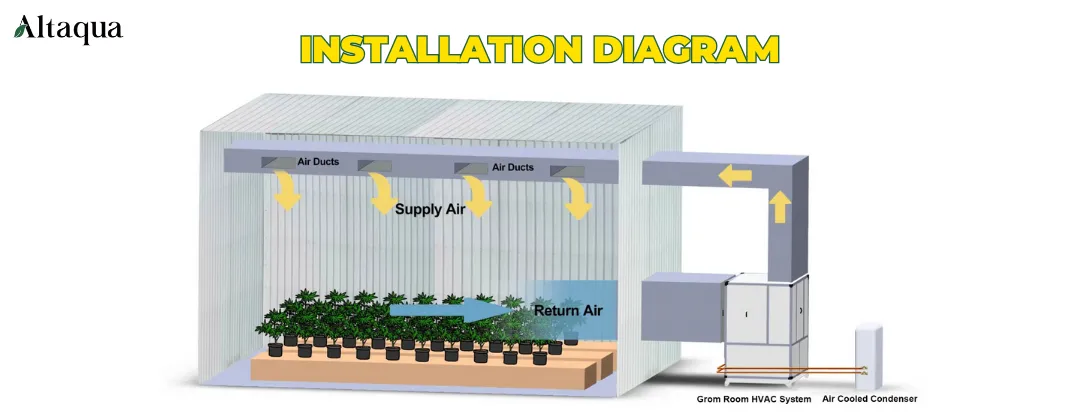
Grasp the Installation Distance
When planning installation distances, you need to consider the installation distances of cannabis HVAC. Growers must consider the layout of the grow room, the available space, and the specific requirements of the HVAC system. For example, equipment that requires additional space for air circulation may need to be kept further away from walls and obstructions.
If the system is too close to a wall or other surface, it may restrict airflow, reduce the overall efficiency of the system, and increase the risk of overheating or humidity imbalances. Proper spacing allows the system to breathe freely, maintain airflow, and effectively cool and ensure a stable environment.
Equipment/Area |
Recommended Safety Distance |
Description |
---|---|---|
Cannabis HVAC to Wall |
2 to 3 feet (60 to 90 cm) |
Ensures proper air circulation around the unit to prevent overheating and improve efficiency. |
Cannabis HVAC to Ceiling |
18 to 24 inches (45 to 60 cm) |
Allows for proper heat dissipation, preventing hot air buildup and maintaining stable temperature and humidity. |
Equipment to Other Systems |
As needed |
Provides adequate space between units to avoid interference and allows for easy maintenance access. |
Reserved Maintenance Space |
3 to 4 feet (90 to 120 cm) |
Ensures there is enough room for regular servicing and emergency repairs, preventing operational difficulties. |
Space for Opening Equipment Panels |
At least 1.5 to 2 feet (45 to 60 cm) |
Ensures easy access for opening panels, facilitating maintenance, inspections, and emergency shutdowns. |
Ensuring the Long-Term Performance and Reliability of Cannabis HVAC
Unlike typical air conditioning systems, cannabis HVAC is required to operate 24 hours a day, and stopping it can have a negative impact on cannabis cultivation. Growers therefore need to take certain measures to ensure that the cannabis HVAC system can operate reliably over the long term.
Equipment Maintenance and Repair
Maintaining cannabis HVAC systems involves not only repairing problems as they arise, but also ensuring long-term performance stability. Regular maintenance checks are essential to identify potential problems before they become serious. For example, filters need to be replaced regularly, air ducts cleaned, and the system checked for wear or faults.
In addition, HVAC systems in cannabis growing environments often need to work more frequently due to constant use, coping with high humidity and regulating temperatures. The more frequently a system is used, the more important it is to schedule regular maintenance. Some HVAC systems have self-diagnostic capabilities that alert you when a component needs maintenance, so you can address the issue before it affects your growing operation.
In the event of a malfunction, a reliable repair service can ensure a quick resolution, minimizing downtime and preventing a negative impact on your plant.
Maintenance Tips for Longevity
Regular maintenance is essential to keep your cannabis HVAC system performing at its best. Here are some key maintenance tips to help extend the lifespan of your equipment:
Regular filter cleaning: Clean or replace filters every 1–3 months to prevent dust and debris from clogging the system.
Check airflow: Ensure all ducts and vents are unobstructed to maintain proper airflow and temperature regulation.
Humidity control calibration: Check and calibrate the humidity control sensor regularly to ensure it is functioning properly.
Monitor energy usage: Keep a close eye on energy consumption and look for sudden spikes that may indicate a malfunction or inefficiency.
Professional maintenance: While some tasks can be completed in-house, scheduling a professional maintenance check at least once a year ensures that the entire system remains in top condition.
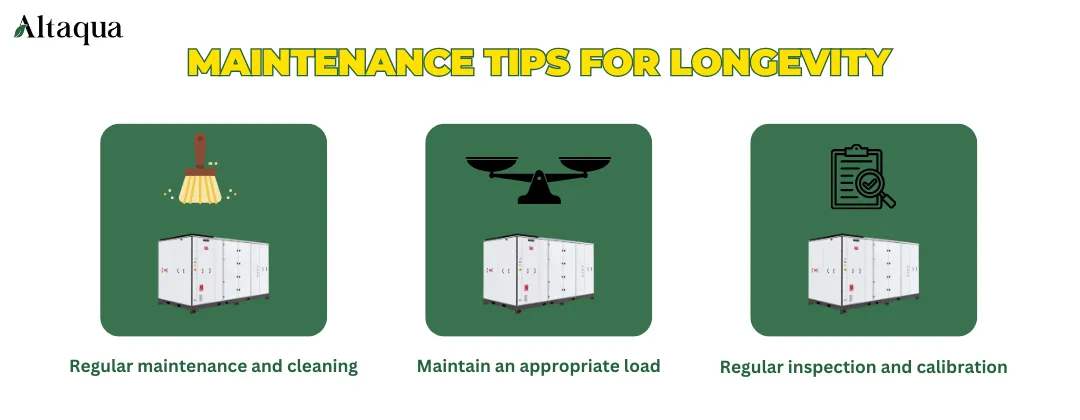
Project and Evaluation with Cannabis HVAC
In this section, we'll explore how Cannabis HVAC systems can impact the overall success of cannabis cultivation projects, especially when compared to other systems like air conditioners and dehumidifiers. By evaluating yield improvement and cost reduction, growers can make informed decisions about their HVAC system choices.
Yield Improvement with Cannabis HVAC vs. AC+Dehumidifier
According to research by Desert Aire, an optimized HVAC system can significantly improve the energy efficiency and crop yield of a grow room. When using a traditional AC + dehumidifier system, humidity control is often not precise enough, which can lead to restricted plant growth. Grow facilities with integrated HVAC systems can improve the overall health and yield of crops through more efficient humidity and temperature control.
For example, a case study found that a grow room with an integrated HVAC system had 35% more energy efficiency per pound of yield and 20% less crop loss over the harvest cycle. One customer achieved more even crop growth by precisely controlling VPD (vapor pressure deficit) with Cannabis HVAC, which ultimately increased revenue per harvest cycle by 25%.
Another significant advantage of these systems is that they help crops adapt better to rapidly changing environmental conditions. For example, during periods of high humidity, while traditional systems may require additional adjustments, integrated HVAC systems can respond in real time over a short period of time, thereby avoiding negative effects on the crop.
Cost Reduction with Cannabis HVAC vs. AC+Dehumidifier
Another significant benefit of using an integrated HVAC system is the substantial cost reduction. According to an analysis by Desert Aire, traditional systems consume about 30% more energy than integrated HVAC systems. This is because traditional AC + dehumidifier systems often need to operate independently and lack synergistic optimization in terms of energy consumption.
For example, one customer saved over $10,000 a month on electricity costs after replacing their system. Over the course of a year, the savings in energy costs more than cover the initial investment in the new system. In addition, the frequency of repairs and maintenance costs are significantly reduced with an integrated system.
According to the report, the annual maintenance costs of an integrated HVAC system are 40% lower than those of a traditional system, and the service life of the customer's equipment is extended by 3-5 years.
By reducing energy consumption and maintenance needs, cannabis-specific HVAC systems not only lower operating costs, but also help achieve sustainability goals. As a result, cannabis HVAC systems are a more cost-effective and environmentally friendly solution for long-term grow room management.
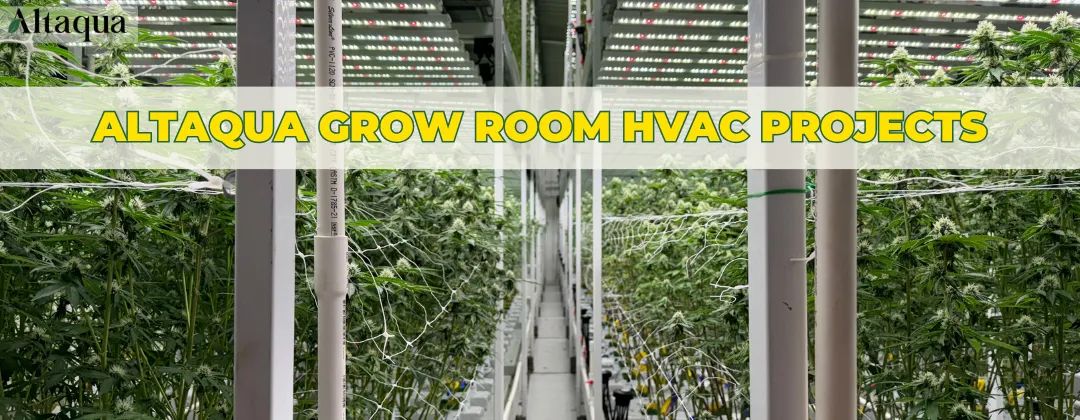
Conclusion
In conclusion, choosing the right HVAC system for cannabis cultivation goes beyond simply regulating temperature and humidity. The benefits of a well-designed system extend far into operational efficiency, yield improvement, and overall energy savings. As we’ve seen throughout this article, systems like integrated cannabis HVAC setups offer more precise control over the growing environment compared to traditional AC and dehumidifier setups. These systems not only streamline temperature and humidity management but also ensure the long-term health of your plants by maintaining optimal conditions throughout the entire cultivation cycle.
The advantages of cannabis HVAC systems are clear when we compare them to other solutions, particularly in terms of energy efficiency and cost savings. Customers who have made the switch to a dedicated HVAC system have reported significant reductions in both operational costs and energy usage. These savings, combined with improvements in yield quality and consistency, underscore the value of investing in a system designed specifically for the needs of indoor cannabis cultivation. Furthermore, the ability to customize the system for specific grow room configurations allows for tailored solutions that meet the exact demands of each operation.
Ultimately, a well-chosen HVAC system is an investment that pays off in the long run. With ongoing support, regular maintenance, and the right installation practices, these systems will deliver reliable performance, ensuring that your growing environment remains stable, efficient, and productive. As more cannabis growers embrace this technology, the positive impacts on cultivation success and profitability become even clearer. By choosing a dedicated HVAC system, cultivators can enhance both the quality of their crops and their bottom line.
FAQ
1. What makes a cannabis HVAC system different from a standard air conditioner or dehumidifier?
A cannabis HVAC system is specifically designed to meet the unique environmental needs of indoor cannabis cultivation. Unlike a standard air conditioner or dehumidifier, which primarily focus on cooling and moisture removal, a cannabis HVAC system provides precise control over both temperature and humidity, ensuring optimal growing conditions for cannabis plants. Additionally, these systems often feature advanced air filtration, CO₂ management, and the ability to adjust settings based on the specific stages of plant growth.
2. How can a cannabis HVAC system improve my cultivation yields?
By maintaining a stable environment with precise control over temperature, humidity, and airflow, a cannabis HVAC system helps create the ideal conditions for plant growth. This results in healthier plants, stronger root systems, and improved nutrient absorption, all of which contribute to higher yields.
3. What are the energy savings associated with using a dedicated cannabis HVAC system?
Cannabis HVAC systems are designed for efficiency, with energy-saving features such as variable-speed fans, humidity controls, and smart sensors that optimize performance based on real-time conditions. Compared to using separate air conditioners and dehumidifiers, these systems can reduce energy consumption by up to 30%, resulting in significant cost savings over time. This efficiency makes the initial investment in a dedicated system more cost-effective in the long run.
4. How much maintenance does a cannabis HVAC system require?
While cannabis HVAC systems are designed for durability, regular maintenance is essential to ensure long-term performance. Maintenance typically includes cleaning filters, checking refrigerant levels, inspecting coils, and monitoring overall system efficiency. With proper care, these systems can last for many years, and many manufacturers offer service plans or recommendations for optimal upkeep.
Share with your friends:
Popular Blogs on Altaqua:
Download Catalogue